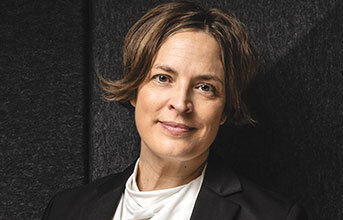
Despite 2023 being a challenging year for manufacturers, global manufacturing output is set to achieve a compound annual growth rate of three per cent between now and 2027, according to technology insight business Interact Analysis. Here, Helen Blomqvist, President of metal cutting tools and manufacturing solutions expert Sandvik Coromant, explores how manufacturers can embrace current industry trends to tackle challenges and remain resilient in 2024 and beyond.
From digitalisation and demand forecasting to economic uncertainty and emissions targets, 2023 presented several challenges for the manufacturing industry. However, these difficulties also provide opportunities for manufacturers to innovate and increase their competitiveness as the industry transforms.
Strengthened sustainability focus
The focus on reducing environmental impact intensified in 2023, with IBM's Institute for Business Value data
showing that 86 per cent of companies now have a sustainability strategy in place. While this figure is promising, data shows that only around a third of businesses have acted on their strategy since its implementation.
2024 will hopefully see the rise of businesses treating sustainability as a priority. This is especially important within the manufacturing industry, which is responsible for one-fifth of global carbon emissions, according to World Economic Forum data. Currently, the sector is not sustainable enough, and we can do a lot more.
Ensuring that sustainability is not just a strategic ambition but a tangible, integrated part of daily operations is key to reducing emissions and achieving green targets. By combining strategic alignment, employee engagement, and continuous data-driven improvements, manufacturers can not only achieve environmental and social goals but also drive innovation, reduce costs, and enhance the company's reputation and competitiveness.
This multifaceted approach is outlined by Sandvik Coromant's new brand promise of Manufacturing Wellness, which aims to drive sustainable progress through impactful partnerships. Manufacturing Wellness is a relentless pursuit of improvement, made up of eight habits found in successful and resilient manufacturing companies. Sustainability and eliminating waste are the third and fourth habits of this mindset, which allows us to drive sustainable progress towards a better tomorrow for people, industry, and society at large.
This commitment is underscored by the recent validation of our net zero target by the Science Based Targets initiative (SBTi). As demand for sustainable products continues to grow, such certifications will become increasingly important for manufacturers looking to stay competitive in a transitioning market.
Developing digital capabilities to meet demand
2023 saw manufacturers feel the aftershocks of several supply chain issues. This particularly impacted the aerospace manufacturing sector, which was still in recovery mode post-pandemic.
However, with demand bouncing back, there has been a revived need from airlines looking to expand or renew their fleets to accommodate the resurgence in passenger travel and meet new environmental standards with more fuel-efficient aircraft. The industry's growth in 2024 will likely depend on how well manufacturers and the broader ecosystem can adapt to these evolving challenges and opportunities.
Aerospace manufacturers can increase their productivity by focusing on resilience, innovation agility, and sustainability. A keyway to achieve this, especially for those involved in metal cutting processes, is to integrate digital manufacturing tools for enhanced operational efficiency. A 2021 study of manufacturing companies conducted on behalf of Sandvik shows that over two-thirds of manufacturers now implement these tools. Use cases include areas such as digital twins, computer numerical control (CNC) integration, process monitoring systems, and cloud computing.
Digital tools support data-driven manufacturing, the fifth of Sandvik Coromant's Manufacturing Wellness habits, which helps businesses spot potential improvements and accelerate productivity from CAD to delivery. Processes informed by data can help improve equipment uptime and extend working life by enabling manufacturers to identify potential failures before they occur. As 2024 progresses, we are likely to see the increased adoption of artificial intelligence (AI) tools to analyse data, with this level of automation helping to meet renewed demand while reducing costs. Incorporating AI tools is a core part of the Manufacturing Wellness mindset, outlined in the second habit of embracing new technology and the eighth habit of automation.
Planning for flexible production
As well as allowing businesses to meet resurgent demand, digital manufacturing tools also facilitate the resource planning process for industries where demand is difficult to predict. This is particularly useful for automakers, who are facing increasing pressure to prepare for the upcoming fossil fuel car phase-out. It is important that manufacturers have sufficient EV capacity in time for the 2035 fossil fuel car ban in the UK and the EU, which has made resource planning difficult.
Data-enabled manufacturing allows for more flexible production systems that can quickly adapt to changes in product design or customer demand, facilitating the production of customised or small-batch items without significant efficiency loss. Integrating digital tools with supply chain management systems can improve forecasting, reduce inventory levels, and enhance coordination with suppliers and customers, leading to a more responsive and efficient supply chain.
As the year progresses, the importance of industry trends such as sustainability, digitalisation, and demand forecasting will continue to grow. However, viewing these challenges as opportunities to innovate will help develop successful, resilient manufacturers that thrive in 2024 and beyond.