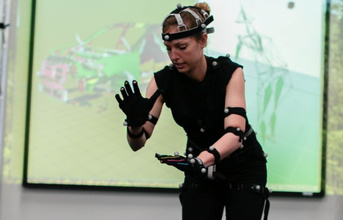
• 3D printing is used by an ergonomist to validate hand clearance in the vehicle assembly process in those instances in which virtual simulation yields unclear results. Employees with various hand sizes use the 3D-printed model to test how tight the space will be in vehicle assembly - which helps to drive better production decisions
• Immersive virtual reality uses a 23-camera motion-capture system and head-mounted display to virtually immerse an employee in a future workstation. Then, the employee's movements are evaluated to determine task feasibility and proficiency
"Motion tracking technology has been used for more than 30 years to quantifiably assess the technique of athletes and reveal where they may be susceptible to injury from overuse or from forces that will damage tissues," said Gary Scheirman, vice president for applications engineering, Motion Analysis Corporation. "Using similar technology, Ford can develop state-of-the-art, safe working environments for its employees and produce better vehicles for its customers."
Virtual manufacturing program results
To date, Ford ergonomists have worked on more than 100 new-vehicle launches globally using virtual manufacturing tools - most recently the 2015 Ford Mustang, F-150, Edge and 2016 Explorer. Through significant investments in the program, not only has Ford achieved a reduction in employee injury rates, it has seen a 90 percent reduction in such ergonomic issues as overextended movements, difficult hand clearance and tasks involving hard-to-install parts.
"Our goal is to provide a healthy, safe and productive work environment at our Ford manufacturing facilities worldwide," said Michael Torolski, Ford executive director, Vehicle Operations Manufacturing Engineering. "The ergonomics and virtual manufacturing processes support our injury reduction strategy and enable early validation of production-technology changes."
End