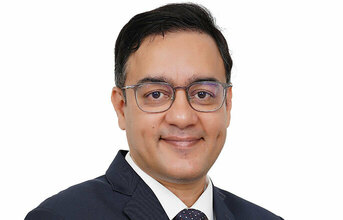
Could you walk us through the journey of Milacron and tell us about how you have seen the company evolve?
Milacron's journey is inspirational and peppered with several innovations. Our story began in 1995 on rented premises, and just a short three years later, its leaders invested in a facility in Vatva, Ahmedabad. Over the years, we've established ourselves as a preferred plastics processing provider for companies across various industries. As of 2023, our India-based facility successfully sold over 25,000 machines.
Currently, we have a manufacturing capacity of several hundred injection moulding machines and a dedicated workforce of over 750 associates. In my 18 months as the Managing Director, I've witnessed outstanding growth in the plastics industry and have subsequently focused on enhancing our production capabilities while increasing customer engagement.
We are also looking at digital transformation through M-Powered, our IIoT (Industrial Internet of Things) solution. M-Powered offers clients sophisticated tools, including predictive analytics, alert reporting, remote technical support, and production recipe management. These tools also are designed to reduce unscheduled downtime.
My goal is to ensure Milacron adapts and evolves to meet industry demands. We prioritise timely and robust service delivery to advance our production, expand our outreach, and embrace advanced digital solutions.
How do you perceive the current demand for plastic processing solutions in the Indian market?
Currently, the demand for injection moulding machines in India stands at around 10,000 machines annually, with a market valuation exceeding Rs 3,000 crore. This demand is expected to continue to increase as the Indian economy grows around 6-7 percent annually for the next five years. Durable plastics are pervasive in our daily lives. From white goods, electronics, automobiles, and CPVC pipes and fittings to packaging containers and medical parts, there is a micro-sample of applications. With urbanisation, digitisation and economic growth continuing, plastics segment is anticipated to grow at GDP + 1.3 to 1.5 percent.
The introduction of production-linked incentive (PLI) schemes in critical end-user sectors is also contributing to domestic growth. These schemes have elicited strong responses from manufacturers, fostering domestic value additions in automotive, mobile, ACs and LEDs, and IT hardware, thereby escalating the need for plastic processing solutions. Moreover, substantial investments by major industry players and supportive policy initiatives fuel this surge in demand.
Taking the automotive sector as an example, it anticipates a significant 19 percent increase in demand for injection moulding machines over the next five years. This surge is not only attributed to the approval of the PLI scheme but is also influenced by the movement toward lightweighting, driven by the shift to electronic vehicles.
Metals are increasingly being replaced by plastics, and a concern for plastics and their harm to the environment remains. Amidst this push and pull factor, how do you see demand for injection moulding machines changing?
We need to create a distinction between single-use plastics (SUP) and durable plastics. SUP and littering are both issues; they need to be tackled by segregation at source and public health policies. On the other hand, durable plastics, which have a typical life span of 10-20 years and are mostly recycled, have played a key role in economic and infrastructure growth.
I would challenge anyone to spend five minutes of their day without touching a part that is injection mpulded—applications in agriculture, greenhouses, auto parts, injectables and disposables in medicine, thin wall packaging for preserving food, appliances, PVC/CPVC pipes and fittings, white goods, furniture, pens, buckets, toothbrushes. The list is endless.
Plastics' versatility extends across sectors. They drive innovation in lightweighting techniques that helps in reducing CO2 emissions within the automotive industry. Likewise, affordable packaging not only helps in reducing food wastages and contamination but also contributes to the preservation of food freshness. In addition, during critical events like the vaccination drive, plastics played a vital role in healthcare equipment, highlighting their significance.
Hence, despite the debates over environmental concerns, plastics are an indispensable part of our industries and lives. As a result, the demand for injection moulding machines will remain driven by diverse industrial needs and technological advancements. For our readers, it is crucial to recognize that India holds the distinction of being the world's largest plastic recycler.
Continue Reading on Page 2