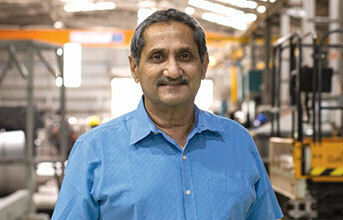
What are the new digital (automation and robotic) technology solutions you offer to your clientele? How is it helping them to revolutionise their manufacturing process and output quality?
We employ digital twin technology, which offers our clientele a revolutionary solution for streamlining their manufacturing processes. By creating a virtual replica of their physical manufacturing systems, including machinery and processes, we enable them to simulate and test changes without any operational downtime. This virtual simulation capability empowers manufacturers to make informed decisions, optimise their processes, and implement improvements rapidly. Traditionally, making changes to manufacturing operations could result in extensive downtime, lasting several months. However, with the adoption of digital twins, this downtime is significantly reduced to a mere 2-3 weeks. By leveraging virtual simulations and implementing virtual changes, our clients can fine-tune their processes, identify bottlenecks, and enhance overall efficiency.
The implementation of digital twins also allows for real-time monitoring and data analysis, providing actionable insights into process performance. This comprehensive understanding enables manufacturers to proactively address potential issues and make data-driven decisions for continuous improvement.
Do you think manufacturers are still hesitant in integrating new age technologies to their facilities? How do you assure them about its benefits and safety?
Manufacturers' hesitation in adopting new-age technologies, like automation, stems from factors such as limited awareness of ROI, uncertainty about benefits, and budget constraints. To address these concerns, we offer comprehensive support by calculating and demonstrating ROI specific to their operations. Our team conducts thorough analysis, emphasising potential gains and cost savings. For those seeking a safer work environment, we emphasise enhanced safety measures rather than ROI. We assure manufacturers of our technologies' adherence to safety standards, providing documentation, certifications, and client testimonials. Our tailored approach aims to alleviate hesitations and empower manufacturers to embrace new technologies for improved facility operations.
How do you ensure compatibility with different manufacturing processes or software platforms?
As system integrators, our solutions are highly customisable to meet specific client requirements. We ensure seamless integration with existing systems and processes without disruption. Considering limitations such as space, footprint, and available resources, we design tailored solutions that address client needs while working within constraints. Compatibility with different manufacturing processes and software platforms is paramount. Through thorough assessments and robust communication, we seamlessly integrate our solutions, optimising efficiency. Our focus is on delivering customised solutions that drive operational success while considering client limitations and objectives.
What advanced technologies do you incorporate into your automation and robotic solutions? How does it help manufacturers to streamline their production operations?
Our automation and robotic solutions are at the forefront of incorporating advanced technologies that are revolutionising the manufacturing industry. The advent of Industry 4.0 has paved the way for the integration of artificial intelligence (AI), machine learning (ML), virtual reality (VR), the industrial internet of things (IIoT), predictive data analytics, augmented reality (AR), and more.
These technologies bring significant benefits to manufacturers, enabling them to streamline their production operations. By leveraging AI and ML, our solutions facilitate real-time data analysis, allowing manufacturers to make informed decisions, optimise processes, and identify areas for improvement. VR and AR technologies play a crucial role in training, maintenance, and troubleshooting. Manufacturers can use VR simulations for immersive training experiences and AR overlays for real-time guidance in complex tasks.
A notable highlight of our solutions is the inclusion of collaborative robots, or cobots, which work alongside human workers in a shared workspace. These cobots enhance efficiency and precision while ensuring a safe working environment. By automating repetitive tasks, they free up human workers to focus on more complex and value-added activities.
Are your automation solutions scalable to accommodate future growth or changes in production requirements?
Our automation solutions are designed with scalability in mind, allowing for future growth and changes in production requirements. By adopting a modular approach, we ensure that our solutions can be easily expanded or modified as needed. From the initial design and construction phase, we factor in the potential for scalability, enabling the addition of more robots, conveyors, or other components to increase throughput in the future.
However, in cases where scalability was not considered during the initial implementation, the feasibility of expanding the line depends on the specific solution. Nonetheless, for most of our solutions, scalability remains possible even after the initial deployment. We prioritise flexibility and adaptability to accommodate our clients' evolving needs and ensure that our automation solutions can grow and adapt alongside their business.