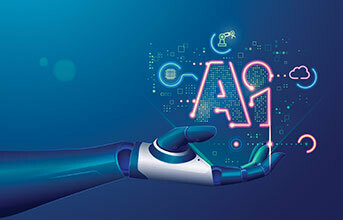
Challenges
Digital manufacturing offers numerous benefits, but it also comes with its fair share of challenges. Some of the key challenges in digital manufacturing include:
Integration Complexity: Integrating various digital technologies, such as IoT devices, cloud computing, AI systems, and data analytics, can be complex and challenging. Ensuring seamless communication and compatibility among these technologies is crucial for their effective functioning.
According to Ranjit Patil, "Integrating automation and robotics into the manufacturing process involves overcoming technical challenges such as establishing seamless communication protocols between the master programmable logic controller (PLC), Message Queuing Telemetry Transport (MQTT) broker, cobot, and Autonomous Mobile Robot (AMR)."
Besides, he also highlighted about addressing compatibility issues, adapt the physical layout to accommodate the new equipment, and ensure safety measures for human-robot collaboration. To address these issues, says Patil, "Tata Technologies implemented advanced algorithms, motion planning techniques, and continuous monitoring, wherein they optimised the system's programming and coordination to enhance efficiency and minimise cycle times." However, through careful planning, rigorous testing, and technical expertise, they successfully integrated automation and robotics into their Smart Manufacturing Lab.
Data Security and Privacy: With the increased use of connected devices and data sharing, manufacturing facilities face heightened concerns about data security and privacy. Protecting sensitive manufacturing data from cyber threats and unauthorised access is paramount.
According to Nitin Bakshi, "Potential vulnerabilities in this era include increased attack surfaces due to IT and operational technology convergence, targeted attacks on IoT endpoints, and the risk of disruption or data theft."
However, to protect sensitive data, intellectual property, and critical manufacturing systems, Bakshi suggests a few best practices including regular patching to address known vulnerabilities, mapping out normal behaviour across industrial infrastructure to detect anomalies, adopting a Défense in Depth approach with layered protection, and fostering collaboration between IT and OT experts.
To mitigate cybersecurity risks, Patil, too suggested a host of measures including robust network security measures, regular assessments and audits, strong access controls, employee education, software updates, data backup, and incident response planning.
Missing Intelligence: Trilogy of Lean, automation and digital go together in all process improvement programs. Automation or digitalisation of sub-optimal processes can impede full realisation of business value.
"While production automation and robots have been part of manufacturing for decades, their limited success can be attributed to missing intelligence," says Rajesh Parameswaran. Typically, "manufacturing automation is based on control systems and programming languages that are not fully capable of adjusting to complex changing conditions, both internal and external. An isolated robot or cell might be efficient in executing its task. But that same robot or cell is not capable of optimising customer orders or substantially impacting the overall equipment effectiveness (OEE) of the whole production facility," he added.
However, "to address this issue at IBM," said Parameswaran, they have been "working towards evolving automation which entails robots and cells connecting and working together in an optimised way." For example, as the automation industry moves toward more open protocols, collaborative robots (cobots) and other transformative enablers flourish.
"Automation facilitates innovations such as lotsize-one, self-healing factories, and putting robots to work in areas where human interaction is required. The latest automation technology can engage in data sharing and co-creation within the manufacturing framework, learning from other units, and enabling plant optimisation," he added.
Job loss and Workforce Skill Gap: The adoption of digital manufacturing requires a skilled and tech-savvy workforce. Many manufacturers face challenges in upskilling or recruiting employees with the necessary expertise to operate and maintain advanced digital systems.
According to Nitin Kalla, the digital transformation of the shopfloor will lead to elimination of jobs in the immediate future, given automation will take over it. However, he is optimistic that "the demand for skilled workforce will rise considerably and this will lead to employees enhancing their skills to be future-ready." Besides, "governments and corporates will have to invest in skilling activities to ensure that many employees are not left stranded on the unemployment highway," Kalla added.
When asked about Industry 4.0's impact on jobs, to which Patil, said, "While automation and new technologies may replace some repetitive tasks, they will also create opportunities for upskilling and transitioning into higher-value roles."
"More emphasis should be laid on workforce development programs which focuses on equipping employees with skills in areas such as data analytics, AI, and robotics," he added. Patil further believes that "rather than resulting in widespread job loss, digital transformation is more likely to reshape job roles and create a demand for a different skill set, fostering career advancement and the creation of new roles."
The future of digital technologies in manufacturing promises a dynamic landscape of progress and transformation. With the maturation and commercial viability of emerging technologies, along with customised solutions and platforms tailored to specific use cases, the potential impact is boundless. The manufacturing supply chain is on the brink of significant disruption and innovation, driven by technologies like Artificial Intelligence, Cognitive Intelligence, Augmented Reality, and quantum computing. These advancements will facilitate faster processing of vast amounts of data and real-time transactions with minimal delays, paving the way for novel operating models and business approaches.