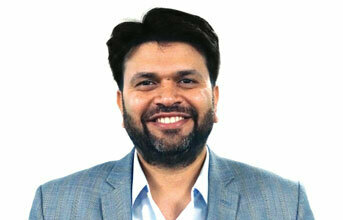
How has Innover inculcated the adoption of digital technologies in the manufacturing sector, and what are some of the strategies you have implemented?
Making use of digital and analytics technologies, Innover is transforming the operations of manufacturing businesses and enabling them to remain competitive in today's rapidly evolving digital landscape.
We have successfully implemented various digital and analytics strategies into the manufacturing processes of leading global enterprises. By harnessing data from diverse sources, we provide valuable and actionable insights. These real-time insights help them to monitor and optimise activities, ensuring uninterrupted operations and efficiency. We have developed sophisticated analytics platforms that gather, cleanse and analyse data from sources within manufacturing facilities to drive accelerated value. The insights from the data provide visibility into production, supply chain, and quality control processes.
Moreover, we integrate AI/ML, IoT, Digital Twins, and Intelligent Automation to connect machines, devices, and sensors across the manufacturing ecosystem, facilitating data exchange and communication. This enables real-time monitoring, predictive maintenance, and quality control of manufacturing equipment. The infusion of automation leads to improved productivity, minimised downtime, and enhanced operational agility. Our industry-centric solutions continuously adapt to new information, enabling decision-making and future-oriented strategies.
How has Innover used AI/ML to combat issues including those of forecasting SKUs, demand predictability and machine breakdowns?
Innover has made significant investments in developing LEAPTM - our Advanced Analytics and AI platform with ready-to-use AI models for the manufacturing sector. LEAP's algorithms have been developed to help manufacturers connect data strands from diverse sources and get insights into the manufacturing process. This helps accelerate data-to-insights-tobusiness outcome journey, ultimately driving tangible impact. Organisations can maintain equilibrium between supply and demand, mitigate unproductivity, safeguard asset health, amplify Overall Equipment Effectiveness (OEE), and optimise scheduling and dispatch.
LEAP analyses real-time data such as production rates, Point-of-sale data, work orders, stock levels, and more to forecast demand at the granular level, thus manufacturers can promptly adjust production schedules, maintain optimal inventory levels, fine-tune workforce planning and make informed decisions on SKU assortments and production volumes.
LEAP's predictive and preventive maintenance capabilities help manufacturers minimise machine outages, enhance asset lifetime expectancy and curtail costs. By analysing historic maintenance data, sensor readings, and other relevant factors, LEAP can identify patterns and anomalies that indicate potential equipment failures or maintenance needs. This can help optimise maintenance schedules, prioritise critical repairs, and provide insights into asset performance.
Can you share any specific success stories of manufacturing clients that have successfully adopted digital technologies with the help of Innover?
One notable success story revolves around a leading global Original Equipment Manufacturer (OEM). The client handled over 100 thousand monthly order requests and faced challenges due to a lack of data-driven workforce planning and allocation. This resulted in idle times, impacting service order fulfillment, revenue leakage, and a weakened brand image. Innover leveraged LEAP to analyse demand patterns, order completion times, peak hours, and other contributing factors; and identified statistically significant time slots for future planning. We assisted the client in developing a robust demand planning and capacity allocation simulator dashboard, enabling swift and accurate insights on field force use. The solution delivered impressive results, including 650 thousand dollars in annual cost savings, a 30 per cent reduction in overtime, and a 16 per cent reduction in employee idle time.
Can you share any examples of industries that have struggled with data quality issues, and what impact has this had on their ability to make informed decisions?
Poor quality data is a pain point for industries spanning from Supply Chain and Manufacturing to Telecommunication and BFSI. Without good quality data, the decision-making process is bound to be adversely impacted with reduction in the reliability of insights and reports.
With respect to supply chains, good quality data can provide end-to-end visibility, intelligent transformation and drive resiliency. It equips supply chains with the much-needed preparedness to face unplanned eventualities caused due to the constantly evolving business environment and global events.
In the manufacturing and logistics realm, good quality data is the guiding light to plan labour, production, and logistics. Good-quality data can optimise operations, upend performance, and build trust across clients, partners, and the industry as a whole. With accurate and timely data on inventory levels, demand forecasts, asset health and supplier performance, manufacturers can optimise their procurement processes, reduce lead times, minimise stock outs or excess inventory, and ensure equipment longevity.
How does Innover approach the challenge of ensuring accurate data quality for its clients, and what kind of services do you offer in this area?
The suite of Data Engineering and Advanced Analytics solutions offered by Innover includes a comprehensive Data Quality framework that ensures the accuracy, consistency, and completeness of critical data sets. Our Data Quality (DQ) Framework empowers organisations to identify high-impact data-related issues across multiple sources to progressively clean and improve the data quality within just 6 - 8 weeks. Powered with a prebuilt AI & ML-based data validation layer, the solution helps businesses automate required checks and balances and identify more than 80 per cent of data processes that are erroneous, inconsistent, or redundant. The framework generates a scorecard, to measure the quality of their data against industry standards, providing a picture of an organisation's current data health and the right steps to incorporate to build a trusted, confident data foundation.
One of our other solutions, LEAPTM, an advanced analytics and AI platform, is designed to expedite the entire data journey for manufacturing organisations, from data capture to valuable insights to facilitate informed business decision-making. It encompasses the entire data-to-value lifecycle, going beyond data quality to include tasks such as data wrangling; establishing tamper-proof, reliable data pipelines; and applying relevant analytical and statistical models to generate insights.
What are some of the key challenges that businesses face when it comes to ensuring data quality for AI/ ML, and how does the DQ Framework help address these challenges?
Businesses encounter a myriad of challenges when striving to maintain data quality in AI/ML initiatives. Some of these challenges include:
Data Accuracy: Businesses struggle to obtain highquality datasets that accurately represent the problem they are trying to solve. Their data may contain errors, biases, anomalies or irrelevant information, which can adversely affect the performance and reliability of AI/ ML models.
Data Completeness: Incomplete data can arise due to various reasons such as human error during data entry, system limitations, or incomplete data integration.
Data Consistency: Ensuring data consistency is a challenge when working with data from multiple sources or diverse business units within an organisation. Inconsistencies in data formats, naming conventions, or definitions can lead to ambiguity and make it challenging to consolidate and analyse data effectively.
Data Timeliness: Outdated or delayed data can impede decision-making and impact business agility. Data must be collected, processed, and made available in a timely manner to real-time insights and facilitate prompt decisions.
Innover's Data Quality Framework helps organisations spot data challenges before they become a menace and progressively improve data quality within just 6-8 weeks. The framework uses AI/ML models to automate data validation, cleansing, and enrichment processes. This helps businesses to help identify and correct errors, standardise data formats, and ensure data is in its prime shape.
What advice would you offer to manufacturing businesses considering adopting digital technologies, and how can they best navigate the complexities of this process?
In this competitive manufacturing market, embracing digital transformation will become imperative for players. When adopting new-age technology, the focus should be on leveraging its potential for innovation and solving business problems.
While implementing a technology, it is essential for businesses to identify compelling use cases and build the right Proof-Of-Concepts (POC) that deliver ROIfocused outcomes. Finally, for a seamless transition to new technology, businesses need to implement effective change management strategies that align the organisation with the technology's requirements. This involves providing training and support to employees, communicating the benefits and goals of technology adoption, and proactively managing any resistance or challenges that may arise. By cultivating a robust talent repository and building a resilient digital ecosystem, powered by data, advanced analytics and contemporary tech, manufacturing organisations can chart a path to data-driven dominance, propelling themselves towards unparalleled growth and prosperity.