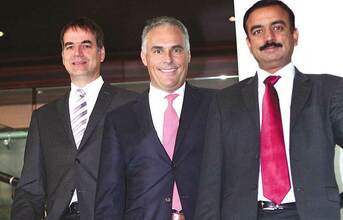
This interview has been published as the Cover Story in the October-November issue of 'The Economic Times Polymers' magazine. ET Polymers is a sister publication of The Machinist.
How important is sustainability for your organisation? How does the recently inaugurated Solar Technologies Demonstration Center contribute in this direction?
Roelof Westerbeek: I cannot stress enough on how important sustainability is for our business. Hundred percent of every euro or dollar or rupee that we invest on research has to do with sustainable development. We do not conduct any research that does not have a better eco footprint compared to the current situation. We also have key performance indicators on how much of our business is sustainable. And we measure that all. It is a combination of corporate citizenship and business drivers. Sustainability is the biggest business driver in engineering plastics.
The latest developments in Pune are a reflection of DSM's ongoing efforts to reduce environmental footprints, both within its own operations and along its value chains. The Pune site is one of the first sites that uses 50 percent renewable energy and we are aiming to increase this ratio further in future.
The site has also reduced its water consumption by two-thirds. With this solar plant, we aim to push our sustainability agenda - which in turn means boosting economic prosperity, environmental quality and social responsibility. We have exactly the same drive behind our market positioning in engineering plastics; our innovation efforts are also focused on sustainable development.
Can you give us some examples of how your innovative solutions are helping the cause of sustainability?
Roelof Westerbeek: One element where we are gathering all our thoughts is the issue of food waste. The world throws away 30 percent of food produced which is 1.5 billion tonnes of food every year. This is absolutely not sustainable. Smart packaging can play an important role in the reduction of food waste.
So we are now having certain programmes in India as well as in other regions to see how we can extend the shelf life of certain vegetables. Mushrooms, for example, have a shelf life of three days. We believe we have certain solutions that can extend the shelf life of mushroom to one week.
And mushrooms are air transported in many places, which is not a very sustainable mode of transport. So if the shelf life of mushrooms can be extended to one week then it can be transported by trucks rather than by air. This will drastically bring down the fuel consumption and make it more sustainable.
Bharath Sesha: In India we have a law that we cannot have permanent warehouses on national highways and most of the food gets transported by the national highways. Due to lack of proper cold storage systems in our country, a lot of this food is damaged.
DSM has these fibre reinforced panels with which we can build warehouses when required and take them off when not required. This is a product that we have not yet launched in India but we are very excited about launching it here because it is the same product that is used to build schools.
According to the Sarvashiksha Abhiyaan, which gives right to education to all, we need to build millions of schools across the country. Many of these schools need to be built in difficult terrains like mountains and deserts where normal construction is very challenging due to various reasons. Using these panels, we can build the schools in three days. In fact, we have already built a school from these panels just outside Pune at a village called Kusgaon.
We have done one more such school in Shahjahanpur in UP and the kids going to that school say that it is much comfortable inside the school during the hot seasons. Thus, for us, sustainability starts with human beings and these small little things make a big difference for us.
We are now talking to many NGOs and the government. We see huge potential for this solution even in the Swacch Bharat Mission where India needs to build millions of toilets.
Roelof Westerbeek: We also have EcoPaXX, a bio-based, high-performance polyamide (PA410) that offers outstanding performance across the board. It is actually made mainly from tropical castor beans. And…it's certified 100 percent carbon neutral from cradle to gate. That means the amount of carbon dioxide emitted during the production of EcoPaXX is offset by the amount absorbed in plant growth.
(Continued on the next page)