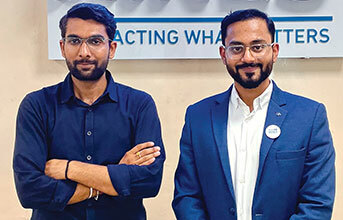
What motivated you to come up with your patented battery recycling mechanism- Hybrid Hydrometallurgy. What sets this technology apart from other conventional methods?
Anupam Kumar: Both me and Arvind are seasoned researchers in the realm of nanomaterials, chemical engineering, and energy storage devices, and we have traversed a remarkable journey in the field for over eight years. Arvind, with a wealth of experience in energy storage devices and chemical extraction, had earned his stripes working on different projects at CSIR-NCL Pune, US Navy-ONRG-Singapore. His tasks involved working on drug development, early detection of malaria, and developing anti-corrosive coatings for naval warships, showcasing his prowess in the intricate domain of materials science.
After the successful product development, Arvind assumed leadership of the R&D department for energy storage and subsequently held the position of AVPR&D at Log9 Materials. During his tenure, he worked on metal-air batteries, supercapacitors, and lithium-ion batteries. This invaluable expertise came in handy for extracting materials, developing chemical processes, and formulating chemistry tailored for li-ion batteries.
Meanwhile, I embarked on my professional journey at the prestigious Bhabha Atomic Research Centre (BARC). There, I researched extensively on extracting uranium metal from the washing liquor of atomic reactors, a task that demanded precision and ingenuity. Eventually, I landed up at Log9 Materials, and contributed to the development of cleanup technology products and business development. Notably, my curiosity and constant urge to innovate led to the creation of a high-efficiency oil sorbent, crucially deployed in mitigating the Mauritius oil spill disaster by the coastguard.
United by our passion for advancing sustainable technologies, both me and Arvind found ourselves at a crossroads. Arvind's work involved making prototypes and discarding used prototype batteries after testing became the catalyst for our entrepreneurial venture. The concept of MiniMines took root when Arvind and I envisioned re-extracting elemental compounds from waste batteries and cells. Drawing upon my prior experience in elemental recovery from nuclear wash liquor, we recognised the pressing need for addressing LIB waste in the energy storage industry.
Fuelled by our shared vision, I and Arvind made the bold decision to leave our well-established positions and set out on a new path. Together, we founded MiniMines, driven by the mission to create a platform for sustainable raw materials, indispensable to produce any energy storage device.
Our timing couldn't have been more auspicious. The escalating demand for lithium-ion batteries, driven by the surge in electric vehicles, portable electronics, and renewable energy storage systems, underscored the urgency of addressing the electronic waste dilemma. MiniMines aimed not just to recycle but to revolutionise the approach towards sustainable raw materials, becoming a beacon of environmental responsibility in the fast-evolving landscape of energy storage technologies.
When we started working on recycling the waste lithium-ion batteries, we started our work from already available technologies like pyrometallurgy, carbothermal and hydrometallurgy solvent extraction. These processes were having different efficiencies and viabilities but were not fulfilling the economic and environmental sustainability parameters. We decided to develop a completely new process, which can cater to the sustainability requirements of LIB recycling. After 2 years of work, we developed a completely new process called Hybrid Hydrometallurgy.
The Li-ion battery recycling technology can be divided into two major technologies:
1. Pyrometallurgical Methods: In this process, the batteries are treated at high temperature (1600- 2000OC), resulting into the conversion of 30 wt per cent carbon in CO2. The resulting material is an amalgam of multiple metals which again requires treatment for the separation into different elemental compounds. This method creates high amount of carbon emissions and is highly unsustainable.
2. Hydrometallurgical Method: This process is one of the most used methods for recycling lithium-ion batteries. It involves the use of chemicals to dissolve metals from the battery electrodes and recover them. The major disadvantages of this method are high energy consumption, environmental impacts, safety risks, limited recovery rates and complexity of the process.
Our USP is our proprietary patented Hybrid Hydrometallurgical TM Method which uses water as a solvent and extract the elemental compounds with more than 96 per cent efficiency and above 99 per cent purity at 1/10th carbon footprint. The process is designed in such a way that it can process all types of Li-ion batteries regardless of their chemistry or form factor. The process does not generate any type of liquid, solid or gaseous discharge during the process making it most sustainable method for recycling.
Kindly elaborate on how this patented method helps in segregation of lithium and other toxic metals from the batteries?
Arvind Bhardwaj: The complete recycling process is proprietary and can be divided into two sections: The first part includes discharging, safely crushing the batteries, extracting Black Mass, and separating aluminium, copper, iron/steel, and plastic. In this part, our proprietary solution deep discharges the batteries for safe disposal. The mechanical crushing is also being done by proprietary machine design, which doesn't generate any PM2.5 or PM10 pollution in the environment.
The second part includes the processing of Black Mass using our patented Hybrid HydrometallurgyTM Process. The Hybrid HydrometallurgyTM Process is based on the principle of the solubility of metal ions in water at different pH, pressure, and temperatures of the solution. The technology comprises 3 segments involving leaching/extraction, elemental separation without using organic solvents, and beneficiation for purification.
How do you ensure the safe handling and disposal of hazardous materials in batteries? What measures do you take to minimise environmental impact during the recycling process?
Anupam Kumar & Arvind Bhardwaj: Our aim is to reduce the amount of greenhouse gas emissions associated with the recycling process, such as those produced by transportation, processing, and waste disposal. By using our proprietary Hybrid Hydrometallurgy process, we are extracting elemental compounds at 1/10th carbon footprint.
Additionally, we are targeting to increase the percentage of Lithium-ion batteries that are recycled, as opposed to being sent to landfills or incinerated. We are increasing our collection capacity every month by minimum of 10 per cent rate, with current collection capacity of 50 tons/month.
The absence of natural resources in India, such as minerals and metals for Lithium-ion batteries can be fulfilled by recovering these materials from waste Lithium-ion batteries. With the proposed capacity by next year, we will be able to cater 20 per cent of national Lithium and Cobalt demand.
According to reports between now and 2030, 11 million metric tons of Li-ion batteries will be dumped into the landfills of which a minuscule fragment of less than 5-6 per cent only will be recycled. How do you look at recovering the minuscule fragment?
Anupam Kumar: The technology is already developed and optimised at a pilot scale. We are currently building a commercial processing plant with a capacity of 3,000 tons/annum.
A product/technology roadmap for MiniMines aims to build a commercial 3000-ton/annum processing facility within the current year and set up three separate hubs at different geo-locations in India for battery collection and black mass extraction.
Are there any benefits or incentives for businesses or individuals who recycle batteries through your program?
Anupam Kumar & Arvind Bhardwaj:
• Employment creation: Our aim is to create 2 jobs for every 5-ton processing capacity in the local community, particularly for individuals who are under-employed or facing employment barriers.
• Reduction in environmental pollution: Our aim is to reduce the amount of waste that goes to landfills and prevent hazardous chemicals from leaching into the soil and water. So far, we have processed more than 1,50,000 batteries and established 6250000 batteries/month processing plant.
• Community engagement and education: We have included more than 500 individuals through the awareness programs and seminars.
• Reduction in greenhouse gas emissions: By using our proprietary Hybrid Hydrometallurgy process, we are extracting elemental compounds at 1/10th carbon footprint.
• Increase in recycling rate: We are increasing our collection capacity every month by a minimum of 10 per cent rate, with a current collection capacity of 50 tons/month.
• Conservation of natural resources: The absence of natural resources in India, such as minerals and metals for Lithium-ion batteries can be fulfilled by recovering these materials from waste Lithium-ion batteries. With the proposed capacity by next year, we will be able to cater to 20 per cent of national Lithium and Cobalt demand.
Are there any upcoming advancements or initiatives in your battery recycling program?
Arvind Bhardwaj: Based on current trends and advancements in technology, it's likely that waste lithiumion battery recycling technology will continue to improve and become more efficient over the next 5-10 years.
Several factors are driving the need for better recycling technologies, including the growing demand for electric vehicles, which rely on lithium-ion batteries, and the need to reduce the environmental impact of battery waste. Many companies and researchers are working on developing new methods and technologies to address these challenges.
One promising approach is the use of advanced chemical processes, such as hybrid hydrometallurgy and controlled pyrometallurgy, which can extract valuable materials from used batteries more effectively than traditional recycling methods. Other approaches we are working on is the use of biological systems, such as bacteria and fungi, to break down battery components and recover valuable metals.
Overall, it's likely that we will see significant advancements in waste lithium-ion battery recycling technology over the next decade, as companies and researchers continue to invest in this area and work towards more sustainable and efficient solutions.
Are there any plans to improve your processes or expand your services in the future?
Anupam Kumar & Arvind Bhardwaj: MiniMines plans to build a 3000-ton processing facility within the current year and three collection hubs in India for battery and black mass extraction, which could be designed as follows:
Research and Development: The first step in the roadmap was to conduct thorough research and development for a sustainable recycling process. This helped us in the identification of the most efficient and cost-effective technology for recycling lithium-ion batteries. After optimising the process for extracting black mass and elemental extraction process development, which is a crucial step in the recycling process, now the R&D activities are focused on optimising scalability of the process, minimising waste, and reducing the overall environmental impact.
Facility Design and Construction: Currently we are designing and constructing the 3000 ton/annum commercial processing facility. The facility is designed to meet the specific requirements of the recycling process, and it is scalable up to 5000 ton/annum for future expansion. The facility is designed to comply with all relevant safety and environmental regulations.
Battery Collection Hubs: The next step in the roadmap is to set up three separate battery collection hubs. These hubs should be strategically located to ensure maximum coverage and convenience for customers. The hubs should be designed to receive, sort, and store batteries before transporting them to the processing facility.
Black Mass Extraction Hubs: The fourth step in the roadmap is to set up three separate black mass extraction hubs. These hubs will be strategically located to ensure maximum efficiency and convenience for the recycling process. The hubs should be designed to receive black mass from the processing facility and extract valuable metals and materials for reuse.