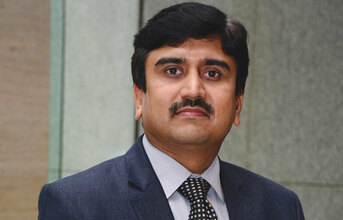
How is MotulTech enabling manufacturers to achieve machine performance and productivity?
We at MotulTech, always put lots of efforts in R&D to give customise products keeping in mind the overall plant efficiency in which machine performance and increased productivity play an important role but there are many more paybacks, which can be shown to customers. One such example is with our semisynthetic water-soluble metal working fluid "SAFKOOL 1044", which was tried against a well-known global company, with the challenge of sump life, smell and skin issues on Makino machine.
We tried for four months and established our product. We have shown that not only did the life of the sump increase from two months to four months but there was also no smell and skin challenge with nine percent improvement in life of cutting tool. All this gave a reduction in oil consumption by 35 percent hence big saving in disposal cost (by 35 percent).
Another example is of our Universelle 800SC, which is chlorine free and vegetable oil based neat deformation oil, where customer has given a challenge of not only improvement in surface finish but also of rust protection for three months. We successfully addressed both of the challenges and increased the productivity substantially, by eliminating the requirement of rust preventive.
How are you helping customers address environmental and safety concerns associated with the use and disposal of oil & lubricants?
As shared above, our aim is to minimise the oil consumption by optimising the customer processes. With this approach we always work to reduce the disposal liability on our customers. Apart from this, we offer products which are globally acceptable and environment friendly even if there is no such law in some cases.
We found that many peoples are still using "Trichloroethylene (TCE)" as cleaning media since it is cost effective, has no fire hazard and is easily available. But they forget that this has been declared as "carcinogenic" if inhaled or swallowed. In the cleaning process, it is allowed to evaporate, hence being inhaled by all the peoples working or visiting the plant.
Most of the times in such cases customer is worried about reduced efficiency, investment and /or fire hazards. We are offering a different approach to such challenges and we map the entire process and give optimum products which can run their plant with same or improved efficiency.
(Continued on the next page)