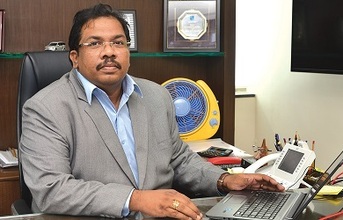
Dr. Goenka mentioned about the implementation of ‘Delivering Customer Delight' and ‘First Time Right' initiatives. How you are pursuing that in the facility?
We have gone beyond the traditional ‘problem-solving' approach; customers expect everything first time right.
To get everything first time right we have automated most of the critical processes, to a large extent, like robotic painting, wind shield glass sealing and fitment, AC, Brake, Power Steering oil filling machines. Where ever we don't have automation, we ensure we have hundreds of POKAYOKE (mistake proofing mechanisms) to avoid any kind human errors even by chance.
Beyond this we have a stringent three tier fire wall/check system to ensure zero slippages to customer. Further on the plant side we have moved from "adherence to specification", to rising up to customer need, meeting specifications is now hygiene.
We have benchmarked global standards and now follow the Global New Overall Audit for Customer (GNOVA C). These daily audits look at every vehicle from today's customer expectations and keep revising the standard and raising the bar.
The aim is avoiding occurrence of any defect in first place through automation, robotics and Pokayoke. Secondly, establishing strong detection systems by way of automated checks at end of the line as well as manual checks. Finally, the most important step, through regular in-sighting into customer expectations and realigning our quality standards. These are the three main elements which help us deliver FTR and ETR products.
We at MVML, take pride in being able to deliver products that delight our customers.
The ‘Design for Assembly' (DFA) - how it is put to practice here in MVML? Please elaborate a little more on it.
Unlike earlier days where we launched one or max 2 products a year, we have moved to an average of 4 to 5 launches a year in recent past, this has necessitated that we crunch time to market from concept to reality.
Most new products have been coming in brown field projects for which their seamless integration into existing production lines and processes is the need of the hour for which this DFA is critical.
There is no time for errors and redos and this calls for early involvement of manufacturing teams right at design stage to ensure smooth implementation. This is where simultaneous engineering and DFA i.e. design for assembly plays a vital role.
Biggest challenge to run a factory is managing costs. What are the measures you undertake for efficient cost management?
As you rightly said, there is increased pressure on us to be cost efficient for maintaining the competitive edge.
The present times call for us to have unprecedented visibility, tracking and control over the entire production process while at the same time creating cost efficiencies.
We have dedicated CFTs in place for every major cost element that builds our cost structure. Idea is to challenge every expenditure and find alternative ways.
We also have central teams across plants who work on power and fuel and look at reduction and alternate source of energy. We presently use wind energy, solar energy and other forms of energy, we also use bio gas which we generate from canteen food waste. We have intershop and interplant working groups on consumables and spare cost synergy. We have centralized buying where it helps take benefits of scale. We also use a lot of technology to aid in cost savings, motion sensors, cameras, robots, cobot, etc.
We regularly do "value stream mapping "to reduce waste and work strongly on "foot print reductions". Both these initiatives have befitted us tremendously in the recent past. For us "Every rupee matters" so while we have big projects, we also have this ideation forum where every associate contributes. On an average, we get 5 to 6 cost ideas per person /year which add to thousands of new ideas flowing into our kitty every month.
(Continued on the next page)