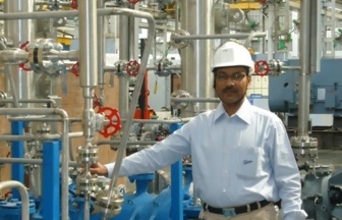
Understanding the customer requirements, statutory & regulatory requirements, applicable codes & standards, and aligning all the processes to meet these requirements, is the key. At KEPL, processes are continually refined based on feedback from various stakeholders including customers, Quality Circle Forum, Kaizen, Statistical Analysis and Corrective Action/ Preventive Action Methodology (CA/ PA), etc."
So what made KEPL choose these systems? "KEPL is a customer centric organisation and is known for reliability. Quality in products, processes, services, documentation and people are part of our deliberated efforts and is a key to excel. Quality systems are helping us differentiate as a reliable organisation. The first API centrifugal pump manufactured by KEPL in 1988-89 and supplied to Bharat Petroleum Corporation Ltd's Mumbai refinery is still working satisfactorily."
KEPL has quality checks at every process level on its shop floor. The hold points are decided depending upon the criticality of the process and communicated through the ‘Inspection & Test Plan' against each item under manufacturing. There are few hold points from customer end at various stages of manufacturing and a few internal hold points including at the vendor end.
People involvement
Of course, any organisation's plan is good as the involvement of its people in making it happen. Little wonder that KEPL is engaging its employees in terms of training and actual operations in ensuring quality. Training needs are identified by respective heads of departments for their team members. "The training is arranged through internal and external faculties on identified areas to improve our employee skills. Employees are involved through Cross-Functional Teams (CFTs) in preparation of Standard Operating Procedure (SOP), analysis, review, counter-measures, refining of SOP through P-D-C-A Cycle or CA/ PA, Quality Circles, Benchmarking, sharing of best practices, etc. This is at all levels from workers to staff to senior management," Katare informs.
During recessions, quality tends to take a backseat for some companies. How does KEPL deal with this? "At KEPL, we are able to avert the trend and effect of recession," says Katare with confidence. And how does he manage this feat? "During all times, KEPL is focused on employee engagement, process improvements, trainings in advanced techniques like Lean and MOST*. We encourage our employees to participate in various contests like QCFI, PDPC, CII Kaizen events, etc. For us, quality is time-less and can never take a back-seat. It is the back-bone of our differentiator ‘Reliability'."