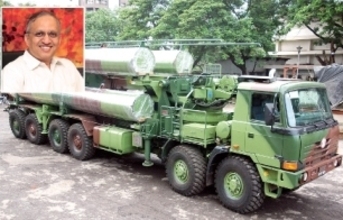
Since defence is a niche segment, has it been challenging to find the right talent in India? Do you have in-house training infrastructure and programmes to address this issue?
The competencies needed to be a successful defence manufacturer are not readily available. So, our focus has been on grooming the talent in-house. Skills, knowledge and attitude help in building the competencies, and hence all are important.
While India is home to a million engineering graduates every year, it is the industry readiness of this vast talent pool that will play a key role in achieving the vision of creating a scalable and sustainable defence industry in India.
A background in mechanical, electrical and electronic engineering or mechatronics, materials (for example, composites) and system integration knowledge is only the start. Engineering talent needs to be trained on the global best practices that will make them competent to meet international standards of quality and safety.
There are various ways in which this knowledge is acquired or created. Our people work with scientists from ISRO and DRDO or specialists from our customer organisations or interact with academia or subject matter experts, when executing projects; and acquire additional experience & knowledge, skills and capabilities during the course of the project. This group then seeds the knowledge to the new members of the team.
Manufacturing for Hi-Tech industry is very regimented; hence there is a sharp focus on translating the knowledge into work instructions. So, we have detailed work instructions for the millions of tasks / operations that are performed on our shop floors for the various projects.
Aided by this evolutionary process, we have been successful in creating a team of highly competent, motivated and enthusiastic operators and engineers. Amongst all types of investments needed - land, building, machinery, capabilities, customer and people - the last three are slow organic processes, and hence, most challenging.
(Continued on the next page)