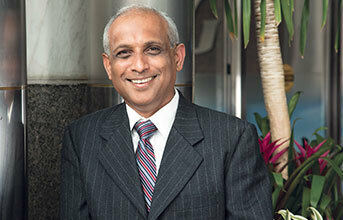
End-to-end (E2E) process design is all the rage in supply chain management and beyond these days. E2E process design delivers efficiency across a work process. So, for instance E2E process design in Order to Cash (O2C), eliminates siloes that create inefficiencies between order management (in the Sales function) and accounts receivables (in the Finance function). Or take an E2E streamlined process that goes from molecule to shelf. That would cut across siloes in R&D (molecule stage), Manufacturing, Planning, and Logistics, and Sales (at the shelf stage). It would result in a super-efficient streamlined work process that ensures information from customers flows backwards not just for supply chain planning and execution, but also to R&D. Such streamlining would cut down the cost of supply chain execution, manufacturing, and out-of-stock losses.
What's not to like about it? I would argue that while there's nothing wrong with this vision, it is good, but not sufficient. It's possible to go even further. In real life execution, we must go beyond E2E "designs" and into E2E unified "accountability".
Unified accountability provides even more business benefits than E2E process design. How? By ensuring that when things unexpectedly go wrong on a day-today basis during execution, there is a human who takes responsibility to address the issue, and to ensure that the overall objective is met. This concept is built into the design of how the aviation industry operates.
Let's study the aviation industry for lessons on unified accountability.
Learning about E2E unified accountability from the aviation industry
If you think that the business processes in your own company are complex, try running an operation that moves 5 billion passengers every year, in roughly 25,000 commercial aircraft, via 15,000 airports located in 195 countries. And do that with over 99.999999 per cent reliability. And just to make things interesting, do it in a decentralised organisational construct where laws, standards, and procedures are not as tightly controllable as within a single company. There is no single CEO-like entity and no hierarchy for single accountability. Yet this is the industry that provides the benchmark for operational reliability. It can teach us important lessons about business process excellence given its decentralised and complex setup.
How has it minimised the defects that occur in handoffs from one team to another? And how does it address the organisation issues of functional silos across thousands of companies?
To help us learn, it might be useful to look at an example of a failure. A post-mortem of a problem, however painful, can often be useful.
Lessons from the Malaysian airlines mg370 disaster
MH370 took off from Kuala Lumpur for Beijing at 12:42 on March 8, 2014. Fariq Hamid, the first officer, was flying the airplane while the pilot Zaharie Ahmad Shah handled the radios.
Thirty-seven minutes into the journey, the flight approached the border of jurisdiction between the Air Traffic Controllers (ATC) in Malaysia and Vietnam. At such borders, control is passed from one ATC to the next via a prescribed handoff process. In line with this, the controller at Kuala Lumpur Center radioed the pilot the coordinates of the Vietnamese ATC: "Malaysian three-seven-zero, contact Ho Chi Minh one-two-zerodecimal-nine. Good night." Zaharie responded with a laconic, "Good night. Malaysian three-seven-zero."
Interestingly, the pilot did not read back the coordinates as required. This is pertinent and was likely related to Zaharie's frame of mind. It was the last word heard from MH370.
The airplane disappeared from the ATC radar a few seconds later. It vanished precisely at the seam of responsibility between the two ATCs, during the handoff process. The next step in ATC handoff would have been for Zaharie to call Vietnam ATC, or, failing that, for the controller to follow up and raise the alarm. These procedures were not followed.
The disappearance of an airplane from ATC radar is extremely unusual. As it happened, the ATC at Kuala Lumpur was busy dealing with other traffic and did not notice it. When he did check later, he assumed that the airplane was out of his range and being safely managed by Ho Chi Minh ATC.
Meanwhile, the Vietnamese ATC, who should have heard from the pilot, tried to contact the airplane, without success. They failed to follow a guideline that requires them to inform the sending ATC if a pilot does not check in within five minutes of being handed off. By the time they contacted the controller at Kuala Lumpur, the plane had been off the radar for 18 minutes.
Further, many of the failsafe processes that should have kicked in, were not followed. Malaysian Aeronautical Rescue Coordination Centre should have been notified within an hour of the disappearance. It was not. It would be four hours before they were notified, by then, it was just too late to help the aircraft.
The key lesson for us in E2E process design is that handoffs are major weak links. The aviation industry builds human accountability (like having the receiving ATC follow-up if the pilot does not check in within 5 minutes). E2E process designs usually don't do that.
Continue reading on page 2