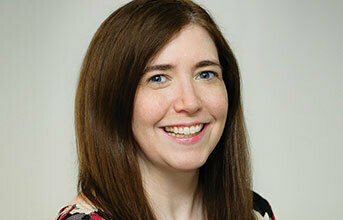
Jana Miller
The new United K i n g d o m headquarters for banking company Santander has combined four existing U.K. offices into one central hub in Milton Keynes, 50 miles north of London. Unity Place will be the workstation for approximately 5,000 Santander employees. The GBP 150 million project connects four new structures constructed on the site of a car park with three atria that maximises natural light in the combined building. The project also adds parking for cars and bicycles on the two basement levels and new landscaping with additional trees and a seating area. Santander chose WSP to help design the project.
Santander has a much broader vision for Unity Place than just as a headquarters for its banking operations. The building would also be one of the first structures that passengers would see as they exit the Milton Keynes rail station, so the organization wanted it to be a showcase and central hub for those who work in, visit, and live in the community. As such, the complex will also feature urban markets, retail outlets, consultation spaces, an auditorium, and health-focused facilities that include a gym and a yoga studio. The roof would be publicly accessible with terraces and a running track. WSP needed to find a way to design a stable structure for the facility without compromising Santander's vision.
Meeting aesthetic and environmental requirements
Santander has specific desires for the aesthetics of the building, resulting in an unusual design.
Though movement joints compensate for thermal movement in buildings caused by concrete shrinking and cracking with time, they were not used for this project. "We were challenged to design a building without any movement joints, as these generally cause double columns to be included, which would significantly affect the aesthetics of the internal layout," said Billy Kelham, structural engineer at WSP. To account for thermal movements during the construction process, WSP had to determine how to implement temporary movement joints to allow for concrete movement, then construct adjacent elements and infill the temporary joints once the team had completed the concrete curing process.
Even with the complexity of the design, WSP had to meet strict environmental standards. To meet the U.K.'s goal that all new builds need to be carbon zero by 2050, the U.K. government established the London Energy Transformation Initiative, a collective of over 1,000 environmental professionals who have stipulated new guidelines and measures for all new buildings to adhere to make that target achievable. These measures include that the total embodied carbon for all non-domestic new builds constructed be less than 600 kilograms per meter squared by 2020 and 350 kilograms by 2030. This is for the building, and includes the structures, mechanical, electric, and plumbing equipment, façade, and architectural finishes. Unity Place had to meet these standards but realized that the traditional office construction of a steel frame supporting metal composite decks would generate far too many emissions due to the high energy involved in manufacturing steel elements. With these challenges, WSP needed advanced structural design capabilities to progress with a concrete frame solution.
Solving issues with structural analysis
The organization realized they could meet all demands of the project by using structural engineering applications from Bentley Systems. They first determined that a concrete superstructure would be preferable to a steel frame, as its construction would generate less carbon. Using RAM Concept, they optimized the post-tensioned concrete slab that were present in the eight-superstructure level during the early stages of the design phase, detailing how to create a safe, and efficiently working slab.
Another example of how the team used Bentley software to improve the efficiency of the design and reduce the level of embodied carbon was visible in the design of the raft foundation. The slab varies in depth between 0.8 meters and 1 meter and bears onto a clay stratum at 10 meters below ground level because of the two-story basement. When clay is unloaded, which happens during the excavation process, it swells causing an upward force referred to as heave. Using geotechnical studies, the team calculated that the heave force was equivalent to 60 kilopascal force but would be fully dissipated after 12 millimeters.
The team used Bentley's RAM Concept to create a heave model of the raft that included the 60-kilopascal upward heave force, but allowed the slab to deflect upwards until it was 12 millimeters or greater. At this point it was known the heave would have fully dissipated. The team reduced the depth of the raft by creating a flexible slab that allowed the heave force to dissipate instead of a rigid structure, which would need to resist the large heave force.
Carrying out geotechnical analysis with PLAXIS by Seequent, the Bentley Subsurface Company, enabled the team to assess the impact of ground movement on adjacent historic infrastructure and services.
Additionally, RAM Concept helped WSP determine how to eliminate the need for temporary eight-piled bases for each of the four tower cranes used during construction. Removing the temporary structures during final slab construction would add time, costs, and energy use. The design team iterated designs and determined how to safely size and place pad foundations to support the cranes until the soil settled under their weight and working loads. These pads were then connected to the rest of the raft and became part of the permanent raft foundation. It is estimated that this method eliminated a total of 32 piles - which would have a concrete tonnage of about 700 tonnes - as well as a saved construction time. They then used RAM Concept to design the ground floor and substructure slabs. The application also established a seamless digital link between WSP's design team and a detailing team in India, shortening the process for marking up plans with design reinforcement requirements from one or two days to near-instantaneously.
Strong design with carbon and cost savings
By using RAM Concept to create the best possible concrete structure design and compensate for the upward heave with the least amount of material, they compensated for the heave force on the raft by using the least amount of material possible. RAM Concept's post-tensioned design capabilities were used to analyse a typical floor plate, which helped to reduce the depth of the concrete slab by 25 millimeters. This reduction over the 53,000 square meters was responsible for saving 3,000 tonnes of concrete and 200 tonnes of carbon. Using post-tension design capabilities, they created a consistent flow rate, further reducing the slab depth to 275 millimeters. As a result, they lowered the amount of concrete needed by 16,000 tonnes, saved significant material costs, and greatly reduced carbon emissions from construction. WSP used the applications to design a raft that bore directly into the clay strata and only supported the two basement levels. Their design greatly lowered the weight of the building, eliminating the need for supporting piles, shortening design time by 50 per cent and saving an additional 2,000 tonnes of concrete. Incorporating the temporary crane supports into the permanent slab prevented the development of 32 temporary pallet foundations, further reducing costs.
By working to eliminate the amount of concrete wherever possible, WSP lowered carbon emissions during construction by 3,000 tonnes, and incorporating the crane foundations into the slab saved another 50 kilograms of emissions. The ability to focus carefully on designing key elements, such as the raft and superstructure slabs, as efficiently as possible helped the building's development reach total carbon emissions of just 219 kilograms of carbon emitted per meter squared for the structure, which is well below the 2030 goal of 228 kilograms of carbon emitted per meter squared, despite only needing to meet the more lenient 2020 goal. "This is a figure we're really proud of and is a joint effort from everyone that's been involved," said Kelham.