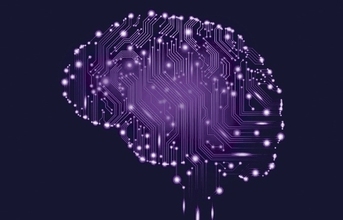
Digitisation is the new currency that can transform the face of manufacturing processes across the world. Manufacturers who are fast in adopting digitally advanced practices are gaining a competitive advantage by exploiting emerging technologies. Digitisation gives a prompt boost to productivity, allowing projects to move faster and helps manufacturers to aim for more aggressive deadlines. Given our country's focus on being self-reliant, we need to quickly develop manufacturing capabilities that can help in the fast delivery and product cycles. Digitisation can help in increasing the pace at which manufacturing activities are performed. Not only this, it also helps in reducing the time for new product introduction and innovation.
There are various factors that have led to this overhaul in the sector, a few being constantly changing consumer preference and new regulations and advances in information technology. Smarter processes like digital twinning, predictive maintenance, and modular design, etc., are contributing the fast adoption of Digitisation. Further on, technologies like internet of things, cyber physical systems, artificial intelligence, big data and cloud computing, will find their application now more than ever. All of this effectively combined with the conventional manufacturing processes and best practices will give rise to smart factories under the framework of Industry 4.0. Smart factories maintain a high output pace, lower the cost and solidify the company's role in an ever-changing market to respond to demand. For example, IoT can help machines to interact with each other, predicting any halt in manufacturing and thus decreasing human intervention redirecting them to more meaningful jobs.
Creating a digital supply chain: Supply Chain 4.0 can also help in making companies more flexible and efficient. Companies need to rethink their supply chains and adopt the new technologies that will help in increasing their productivity. The application of the Internet of Things, the use of advanced robotics, and the application of big data can all lead to this. For example, placing sensors to track the goods, creation of networks among processes and automation can help in analysing these processes and can significantly improve efficiency and customer satisfaction.
Artificial Intelligence and Machine Learning can be used to understand consumer behaviour and design products accordingly. During a crisis such as the current coronavirus pandemic, a smart factory can be run and accessed remotely with minimal human intervention at the site. While adopting such advance technologies, companies should also be mindful of equipping the manpower with necessary skills and knowledge. This is essential to provide them with a stable employment and requisite livelihood benefits. They can also be trained to operate and manage these smart factories which will involve robotics and software applications.
Augmented Reality (AR) can further be leveraged to increase the efficiency of operations by reducing production downtime. For instance, through AR, a professional sitting anywhere around the world can guide a technician present on the ground on various issues related to machinery and operations. It can also help in reducing errors and can be used to train the workers on the plant floor, remotely. A single plant head can help managing multiple plants through the help of AR. It can play a major role in product design and development as well. Conceptualisation, prototyping, and traditional design thinking can be very lengthy and resource-intensive processes. Through AR, one can give an overview of the actual product being designed and constructed on a real-time basis. This can provide insights and direction that would eliminate the trial and error and resources spent in actual manufacturing of prototypes.
The above mentioned changes are not the end of digital transformation as we move to manufacturing 4.0, it is a critical start. Once simple processes are digitised, then additional technologies like machine learning, artificial intelligence, Internet of Things, digital twins, and a comprehensive, complete digital strategy can emerge. But we have to take the first steps to start thinking digitally. This will help in giving real-time insights that one can access and use to make business decisions that will, in fact, transform businesses in India.
END