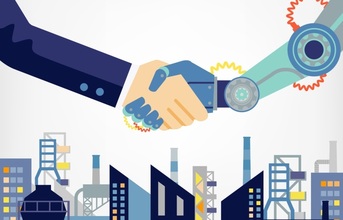
Innovative concepts in Industry 4.0 can provide optimum support in predictive maintenance.
The manufacturing industry is extremely asset-driven. With increased customer demands in an ever-growing competitive landscape, manufacturers can no longer let the threat of a machine breakdown affect their production. To achieve Industry 4.0 and to prepare for a future where smart machines accelerate overall business success, manufacturers are increasingly focusing on predictive maintenance, remote monitoring and asset management issues.
Shortcoming and opportunities can come into sharp focus, along with commitments to improve and the funding to make it happen. For plant maintenance teams, a high volume of emergency service requests is frequently a top issue. Jumping from one urgent work order to the next is highly inefficient and disruptive. Fortunately, technology can help manufacturers turn over a new leaf and strive for a more proactive approach to maintenance. Predictive maintenance is becoming an integral focus in manufacturing industries to obtain operational efficiencies of equipment. Since the consequences of machine failures are too high, this ability to identify patterns and forecast potential equipment failure allows manufacturers to optimise equipment lifetime and minimise unplanned downtime.
Digitalization to lay the foundation
Today, maintenance is seen as a key priority in the manufacturing companies, in India, keeping the opportunity to digitally transform the business. Once a plant is in reactive mode and is chasing emergencies, it is hard to get in front of the issue, especially if the equipment is past its prime. Manufacturers often had to make do with outdated assets and patched solutions. Factories hungry for growth are racing to adopt digital technologies and deploy advanced innovations to increase responsiveness, agility, and customer engagement.
Digitalization will lay a foundation for improved productivity and reliability. Innovative concepts in Industry 4.0 can provide optimum support in predictive maintenance. The accelerating pace of technological adoption significantly reduces man-hours on maintenance, decreasing machine downtimes and repair time, constantly improving the production flow. The power of technologies and solutions such as 3D-printing, virtual reality, augmented reality, cloud computing, AI, IoT, with ERP, supply chain management and enterprise asset management (EAM) provide a competitive edge in addressing manufacturing needs in various areas of maintenance, production and warehouse management.
Being proactive
In the age of digital transformation, EAM solutions eliminate silos and increase productivity across the company. It focuses on capturing data, analysing the data across assets and acting on the insights of the data for asset maintenance, a three- step dynamic condition-monitoring framework.
Enterprises are rolling out new customer-centric services - new partnerships are on the horizon, and key Internet of Things (IoT) and Artificial Intelligence (AI) initiatives are being tested. It is more important than ever that machinery and equipment perform as needed. It is a high-stakes landscape. No company wants to risk highly-visible disruptions damaging credibility while in the midst of negotiating a merger or signing a multi-year customer contract.
This is why turning to proactive asset maintenance and Condition-Based Monitoring (CBM) is so important today. Manufacturers on the cusp of a new era need their machinery operating at peak performance. If current systems are performing as needed, technicians can focus on other priorities such as new deployments, embracing sensor technology, reducing waste, improving sustainability and scaling for expansion.
Where to begin?
EAM solutions are a necessity to tracking and monitoring complex plant assets. The more complex the asset, the more critical it is for systems to help manage the high-tech components. Computerized machinery with digital displays, built-in safety protocols, voice recognition and AI-assisted functionality often require version upgrades. Security updates and data back-ups are other ongoing tasks that modern cloud-connected equipment, like robotics, may require. Yesterday's maintenance solution will be ill-equipped to keep pace with the challenges.
Modern EAM solutions, though, bring a wealth of features which make proactive equipment service feasible. Manufacturers can up-level their goals and re-set expectations, focusing on prevention rather than repair.
Final takeaway
Manufacturers are in a pivotal position. Opportunities for growth are within reach as market conditions improve and digital technologies promise to unlock new revenue models, automation, and customer alignment. Delays from unexpected downtime and the need for frequent emergency repairs can easily become a drain on the organization—just when optimal performance is needed most. From gathering data to asset management, adopting next-gen technologies are practical and critical to scale reliability, optimize operations and initial machinery investment. Asset management in any commercial or industrial organization—can help manufacturers run their equipment more efficiently and add longevity to those units by adding years to the life of assets. Setting resolutions to be more proactive will help the asset maintenance team make better use of resources, helping the enterprise feel confident about its critical shop floor equipment.
END
The author is Director, Solution Consulting, Infor India
For useful demos and essential reading, visit https://www.themachinist.in/infor