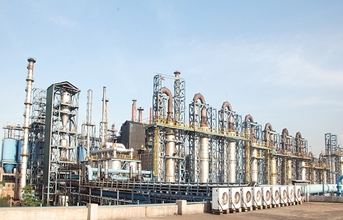
When the WCM framework was formulated in 1995, the biggest challenge was how the units would implement TPM and what their assessment parameters would be.
Hence, an extensive training program was organised. It comprised of a ‘WCM Kick-off' where a WCM Road-Map was discussed and each unit was given guidelines and a charter to follow.
It also required forming of cross-functional sub-committees within the unit that helped check the quality of manufacturing from time to time. After the new framework was formed in 2010, CBE started following a similar orientation process for its employees.
The goals, though, had changed. Assessment was at the business level rather than on an operation level. The CEO of the business would chair the steering committee.
It had several smaller groups such as the Customer Focus Group, People Focus Group, Operations and Finance, Projects Finance and Strategic Finance to measure the parameters of excellence.
The scenario had changed over the years with changing demands of the consumers. The Corporate Business Excellence Cell was set up to cover the end to end processes of every business.
As Ramaswamy aptly puts it, ‘It wasn't about customer satisfaction any more. It was about customer experience." An excellence framework pushes for commitment and a drive to perform better. What transpires in the attempt to achieve this feat is an enormous commitment to quality.
Birla Cellulose, Aditya Birla Insulators, Thai Acrylic Fibre, Essel Mining and Novelis are a few notable examples who keep the flag of CBE flying high by implementing the best manufacturing practices in their daily functions.
The VSF quality parameters at Birla Cellulose are measured on a daily and hourly basis. Besides conducting internal quality checks, they are constantly compared to international benchmarks such as Critical to Quality (CTQ) and Statistical Process Control (SPC). As a result, Birla Cellulose has been recognised for its efforts. The coveted Deming Quality Control Award in 2003 was awarded to the Kharach unit and it continues to weave magic years later.
Novelis' ‘One' approach philosophy is practiced internally. Novelis is the world's largest recycler of aluminum beverage cans and recycles approximately 40 billion cans annually which are critical to its operations with recycling being the core element of their manufacturing process.
Its rolled aluminium manufacturing process focuses on excellence and sustainability. The commitment is not just an environmental mandate, according to Novelis, "it strikes the very heart of the Group's corporate philosophy."
The CBE Cell constantly looks at innovating according to the shift in the manufacturing scene by regularly attending seminars, talks and staying updated. Every two years the guidelines are upgraded and in doing so, pushing the businesses to raise the bar.
While the excellence model forms a guideline for the businesses, there are other key initiatives that the Group as a whole undertakes to promote the use of best practices.
(Continued on the next page)