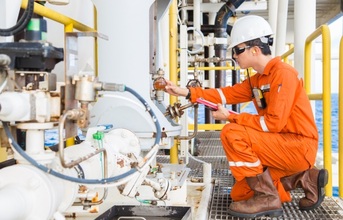
The two most important considerations in managing your lubrication program are - selecting the right lubricant and selecting the right delivery system. In this article, we will describe all the major types of automatic lubrication systems that are used by the plant managers around the world, so that you can make an informed choice.
Manual Lubrication
Firstly let's take a look at the alternative to Automatic lubrication - Manual lubrication. It is carried out for a large number of greasing points in many companies. The last 15 years have seen significant progress in the field of manual lubrication. Cordless grease guns, grease meters and Computer monitored greasing systems equipped with radio-frequency identification technology (RFID) have greatly eased the lubrication technician's work. Some systems have also been designed to use acoustic aids for sensing if the lubricant has reached till the rolling edge of the bearing.
Manual lubrication has become increasingly reliable thanks to all of these products. Counting strokes form a manual grease gun and hoping to obtain a correct amount is an outdated practice for lubrication technicians today. Technicians should always be facilitated with a grease meter and if you have a large production plant with many lube points, consider getting cordless grease guns.
Automatic Lubrication Systems
If manual lubrication system is inadequate for your plant's lubrication requirements, you can have an Automatic lubrication system. It is much more efficient than manual labour and hence it greatly reduces cost; it eliminates the chances of over lubrication and under-lubrication and minimizes the risk of contamination. Its benefits are elaborated here.
An automatic lubrication system can have several types of configurations like - dual line system, single line volumetric system, single-line progressive system or a single point system.
Dual-Line Systems
Heavy processes industries predominantly use dual-line lubrication systems as they are very reliable, simple to understand and easy to maintain. It is also relatively easy to increase or decrease the number of points in such a system.
This type of system is called a dual-line lubrication system as it uses two main lines for lubrication. The lubrication occurs as all of the distributors of the system are pressurized together, creating high pressure towards the feeders. Unlike single line systems, the pistons are not spring-loaded; they just initiate the second delivery stroke to "reset", like in the spring-loaded pistons. This mechanism takes place under full pump pressure and hence it is suitable for lubricants with high viscosity. They are also available with compressive seals for heavy-duty operating conditions.
Single-Line Volumetric Systems
This type of lubrication systems requires only one main line. They are ideal for oil lubrication and some of them are designed specifically for grease. Much like the dual line lubricating systems, single line systems are simple to understand, easy to maintain and easy to increase or decrease the number of points in the system.
The dispenser in this system reloads after every cycle of lubrication and hence, the piston in the dispenser has to overcome the pressure of lubricant inside the pump line. There are models of this system that are specifically designed for grease lubrication. These models are capable of reloading the dispenser at higher venting pressures due to their strong springs.
Single-Line Progressive Systems
The most important component of a single-line progressive system is its progressive divider. A fixed amount of grease is fed from one end to the other, using a hydraulically driven spool from at least three dispensing elements. The length and diameter of the piston stroke determines the volume of lubricant, hence it cannot be adjusted. The internal connection of spools is done through cross-porting arrangement which forces the spools to work in a sequence. If anytime in the process, one spool is not able to complete its stroke, the divider stops working.
The single-line progressive systems are often designed with a single primary divider and multiple secondary dividers. Hence, monitoring a spool in any of the drivers gives you total control over the whole system, if the tube doesn't have leakage from the divider to the wear surface.
Single-Point Systems
Single-point lubrication systems originally consisted of a spring-loaded piston which was charged with grease. Grease was extruded through an orifice, due to the spring force, dependent flow on the orifice and the stiffness of the grease. This spring-activated model was not adequately efficient; hence it only had a limited impact on the market.
Single-Point Lubricators
The last 20 years have seen some major improvements in single-point lubricators (SPLs). They are now easy to install and they do not require major financial investments. The unit can simply be screwed to the lube point, and you can set the operation time to start it. Operation time can generally be set form 1 month to 12 months. While managing single-point lubricators may sound easy; they are easily ruined if the technician is not knowledgeable about these devices.
Single-point lubricators come in three basic models, spring-activated, motor-driven and gas activated.
The spring-activated SPL contains a piston pump that sucks lubricant from the container and feeds it out directly. It can create pressures of 425 to 850 psi, which is 30 to 60 bar.
The motor-driven SPLs have a piston with an electric-motor-driven mechanism placed over the container. The mechanism uses steam to force the piston into the container, which makes the lubricant flow out. The motor-driven SPLs usually reach much lower pressures then spring-activated versions; they have a normal pressure of 72 to 145 psi, which is 5 to 10 bar.
The third type of SPL is the gas-activated SPL; it involves expansion of a gas using a chemical reaction. The reaction is initiated by introducing a gas generator in the electrolyte fluid. The pressure of gas expansion is transferred to the lubricant inside the container and this forces the lubricant to flow out through the lube point. This system reaches the maximum pressure at only about 75 psi (5 bar), but it can even be as low as 15 psi (1.5 bar) in some models.
Using single-point lubrication system of any type requires used lubricator as waste or treating batteries. This waste should be properly disposed and its disposal system should be considered while choosing the equipment to be used.