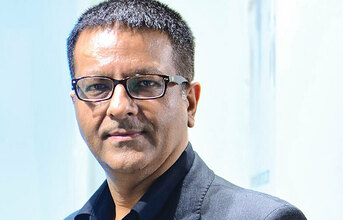
A major focus of the CAD/CAM industry, currently, is bridging the gap between subtractive and additive manufacturing. Another area of growing interest is the use of Industrial Robots for applications like milling, tape-laying and laser cutting. Companies like us have already created an ecosystem around the product to help independent players to build innovative products on the programming interface offered by Mastercam.
On the business front, CAD/CAM industry was facing an inevitable consolidation - which started happening post the 2008 slow-down, and continues even today - resulting in many well-known brands merging with others. Obviously, this means that there will be a further consolidation in products and services.
An integrated CAD/CAM system is one, in which various modules, for e.g., Turning, Milling, Mill-Turn, WireEDM, etc., are operational within the same window and within the same interface. In all, an integrated CAD/CAM solution provides a unified interface, which helps boost productivity, reduce training efforts, as well as streamline toolpath generation process.
A full-featured CAD/CAM program like Mastercam can have more than 800 separate functions, each with its own name and icon. Whatever the challenge, there is likely to be a function in the CAD/CAM toolbox that can assist and make the job easier. On the other hand, accessing a particular function from such an expansive tool set can be like searching for a needle in a haystack. A well designed integrated CAD/CAM interface enables features, that users require routinely, and puts them at their fingertips, while making it easy to identify and activate features that are needed less frequently but also boost precision and productivity when they are called for.
A Hybrid manufacturing method is technically more complex than the current method of cutting shapes from blocks of metal. CAD/CAM will continue to play, in fact, an even more significant role in the Hybrid manufacturing process. Beginning with designing
the near net shape, support structures and 3D build process plan, CAD/CAM software will control the entire process ending with the final shape being cut with codes generated by CAM software, on the near-net shape as input model reference.
The benefits of such processes will be - reducing the carbon foot-print, achieving conformal shapes, reducing machining efforts, reducing material scrap and in light-weighting solutions - to name a few.
Role of CAM in Industry 4.0
CAM software will be an active component of the total manufacturing solutions within Industry 4.0 implementation. Various knowledge based inputs will be fed in into the CAM system, thereby allowing the right parameters to be used for the right machine environment. The output too, can be provided to a middle-ware that processes outputs for different machines, for the same component, if need be. Just in time programming could be a possibility provided a closed-loop can be established with machining time, enabling optimisation in the CAM process.
It is vital for manufacturing companies to invest in the right CAM software. A CAM system for complex machining must have the following capabilities -
• Accurately import and/or repair CAD models from various CAD systems.
• Simple to learn & easy to use, yet powerful enough to achieve the most complex task.
• High Speed & High Efficiency Machining Routines
• Multi Axis Strategies with advanced configuration options & Machine simulation
• Speed for toolpath processing, and post processing
• Support for all machine tools & controllers, especially in Post Processing
• Output Gouge/Collision free toolpaths
• Customisable (with API) for advanced and bespoke application development for power users.
Tool utilization factor is of paramount importance, considering that longer the tool life, higher the productivity. Therefore, modern strategies that assist in deriving full tool life are a must in CAM software, than those that are traditional.
This article written by Vineet Seth who is the Managing Director, Mastercam APAC
END