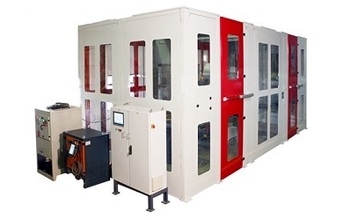
Robotic Automation
Robotic Automation is the use of Industrial Robots to automate and standardise repeatable manufacturing processes/tasks. Automation of this process brings several key benefits to the manufacturers of castings like increase in productivity, upgradation in quality, healthy and safe working atmosphere. The technology behind Robotic Fettling and how it may be successfully deployed across the iron casting industry serves as a guide of dos and don'ts for good executions. Iron castings of manufactured parts, as you are all aware, have the most complex shapes. And here is where automated robots come to the rescue by delivering quality with accuracy down to the last thou (a thousandth of an inch).
With the advent of this new revolutionary technology, Robotic Fettling for Iron Castings will see the sector in an upswing. Using automated robots brings enhanced benefits including an up to eight-fold increase in productivity, exceptional quality that meets international standards and safe working environment while exceeding client's expectations.
The advanced systems built by Grind Master for fettling operations including riser and gate cutting, parting line grinding, de-burring sharp edges, milling inaccessible areas and breaking into holes. Robotic iron casting fettling technology addresses key issues that show up such as effectively managing complex shapes/heavy components, reducing hazardous working conditions, heavy stock removal, variety in component geometry, with manual/automatic load, unload using pallet exchangers, automatic tool changer, automatic path corrections, dust collector system and more. The Critical challenges overcome by the system include -
Optimization of Light Weight Parts
Lightweighting has resulted in optimized designs of castings whereas inconsistency in fettling leaves marks, scratches, dents etc on surfaces. These can result in fatigue failure of the part where consistency in fettling is essential for manufacturing such to have aesthetic value.
Production Volumes - Part Variants
Many ironcasting components are made in medium volumes of maybe 100 parts/day where any automation system is scalable, fast producing and extremely reliable to cater to this requirement. It should accommodate multiple part variants in the same system with quick setup change, simple fixturing and easy part programming are essential for this.
Component - Component Variations
Fettling operation is done on as cast parts, which have part-to-part variations inherent to the casting process where these variations pose challenges in Fettling Automation - starting from location and fixturing, to uniformity of force applied during fettling, to making adjustments for part variations.
Robotic Fettling - Tool Selection
Robotic Fettling Systems arrangement is a combination of tools for completing the requirements. A knowledgeable system integrator is able to choose wisely the tools used for a specific job requirement. Tool Selection is critical because the process reliability, cycle time and running cost of the system are majorly based on the type of tools used. In certain cases, it is observed that selecting the most advantageous tool can reduce cycle time and cost running by as much as 90%. The most commonly used tools in Robotic Fettling include diamond-plated wheels for cutting and grinding.
Robotic Fettling - Quality Improvements
Robotic Fettling gives tremendous improvements in the consistency and completeness of fettling. Manual operations are subject to numerous variations through the days, weeks and months of the year where more than one operator never works in the same style. Multiple operators work on one component leading to handling damages. Cutting tools manually operated invariably causing scratch marks, dents; dig into unwanted areas, which are a major cause for rejection of castings.
Robotic Fettling - Cost of Operations and Economic Feasibility
Robotic Automation Systems have various costs associated with them, which have to be considered while calculating cost per piece over the long run such as the maintenance costs (Annual Maintenance, Spares etc), energy costs, consumables costs (use of customised tools for robotic application can save significantly); retooling, reprogramming costs and labour costs (including future rise in the same). Significant improvement in quality is considered while calculating the investment returns of a robotic fettling system. A drastic reduction in rejection rate and removal of rework/checking stations also brings space savings. Correct selection of application and wise implementation can ensure a Return on Investment of Robotic Fettling Systems within 2 years.
(Continued on the next page)