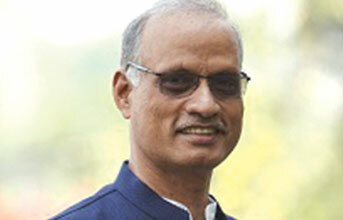
In a manufacturing shop floor, there are a series of sequential value-adding operations carried out to deliver a finished product ready for customer consumption. This value flow process can be executed using a single-piece flow (SPF) (one-piece flows through a series of operations adjacent to each other) or a batch flow (BF) approach (flow of two or more pieces in a batch through the operations). Motorcycle assembly on an assembly line is an example of a single-piece flow, while washing and drying processes for a batch of 5-7 dirty clothes exemplify batch flow processing. Each flow approach has its pros and cons.
As a young disciple of lean manufacturing, I learned that SPF on shop floors is always beneficial. It facilitates material flow, space optimisation, and inventory control, thereby reducing operational costs.
It was shared that SPF is characterised by its speed, as waiting time per piece is negligible, thereby meeting customer needs faster and facilitating high equipment utilisation. It moves inventory faster, enhancing the stock turn ratio (STR) and reduces lead time, thereby improving responsiveness to customers. It also exposes quality issues quicker, only to be resolved, thereby mitigating customers' quality concerns. Lower labour costs and overheads are other important features of SPF. However, the characteristics of the BF are weak in each of these factors. The explanations were logical and convincing to me.
In real life, after studying many manufacturing setups, one finds that most manufacturing shop floors practice batch flow systems. The bakery kitchen, beer processing, washing and drying processes, garment production, soap manufacturing, sheet metal surface treatment method, heat treatment of components, R & D, and many more have a batch-dominant flow.
What made them not follow a single-piece flow which had benefits? It is also worthwhile mentioning here that in the futuristic smart factories, driven by Industry-4.0-related technologies, quality, setup change duration, inventory tracking, material handling, volume scaling, Overall equipment effectiveness (OEE), and many other production issues will be low concern areas. This justifies the exploration of a detailed and deeper understanding.
There are many positives in running batch flow production:
• Focus, care, and inspection by a specialist operator for each operation of the entire batch of parts ensures superior quality of the product. The specialist operator is always skilled and takes reasonable time, unlike in single-piece flow. BF also facilitates operational rhythm. Envisage a batch of gears on a large pallet being inspected by an operator.
• Traceability of operation and control of inventory is better in batch flow. Based on the customer demand forecast, the size of the batch can be defined.
• Movement of a batch from one operation to another is more cost-effective than ensuring a single piece flow, one after the other covering all operations. Flow-related investment in BF is likely to be lower.
Batch flow facilitates more effective purchasing due to bulk ordering. Batch flow is apt and preferred in most manufacturing shops when:
• Subsequent or the next operation in the value chain is physically far-spaced,
• The shelf-life of the finished product is short.
• Reliability of the equipment(s) is a bottleneck
• Variety in the product family is high
• Seasonality factor in demand exists
• Initial set-up cost for single piece flow is economically not viable,
• Transportation of a single piece is significantly higher than batch material handling,
• Subsequent operation is not in the vicinity/ next to the last operation (process limitation)
It is often said that SPF production is simple in operation, smooth in flow, and consistent in delivery. This is a perception. A deeper analysis indicates that the eight lean-related wastes (DOWNTIME- an acronym for eight wastes) in manufacturing, hamper the smooth flow. Process variations like rejections, rework, material shortage, not-right-first-time, machine breakdowns, absenteeism of skilled labour, supplier quality defects, and others prevent streamlined flows. BF production processes can also be simple, smooth, and consistent if the process variations are eliminated. It is the low variation that drives the positive perception of SPF, which is feasible in BF too. This leads to the need for implementing the Six Sigma approach to reduce variation and smoothen the flow, be it SPF or BF.
One key area to focus on is always to have a manufacturing system that takes advantage of both the SPF and BF. This can happen in Cellular manufacturing systems. However, it demands quicker setup change time to improve the OEE, reduce lead time, and enhance STR, preventing large batch sizes.
In summary, single-piece flow has many benefits in product manufacturing. However, it is not a cure for all issues in manufacturing. Furthermore, its implementation makes little sense in most production situations in the current world driven by high product variety, varying market demand, short end-of-life of products, and production in technology-driven reliable machines. The key decision point lies in the economic viability of the production flow system. Therefore, think-analyse and embrace the right production system in your manufacturing shop.