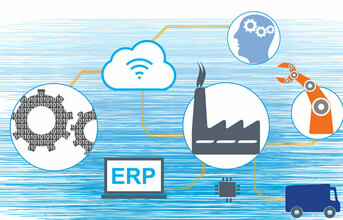
The fourth phase of the industrial revolution or Industry 4.0 is fundamentally changing the way a wide variety of industries are working. From procurement to distribution, through manufacturing and till the finished products, processes are being automated to be more efficient, lean, agile and with higher quality. It is indeed a revolution, since it has come very fast, is changing the entire industry and it is a global activity.
The first industrial revolution was the shift to new manufacturing processes and mechanization. Moving from hand tools to machines, mechanised textile production, and the rise of the factory system. The second industrial revolution, also known as the technological revolution, was a period of rapid industrialization with advancements in manufacturing and production technology. It came in the early 20th century, when Henry Ford mastered the moving assembly line. This ushered in an age of mass production. The third industrial revolution was the advent of the digitalisation and green electricity that resulted in laying out the basis for a sustainable global economy.
The overtaking of people-centric roles by robotics, automation and intelligent sensors leads to faster and better ways of working, limited or no errors in production and highly durable systems that increase production output. This may seem like it leaves no room for individuals to participate in industrial activities anymore. Labour seems questionable in these circumstances. Some sources expect disruptive improvements in terms of quality, productivity and customer orientation; others are concerned with job losses, high costs for investments and data security.
Industry 4.0 - An invitation to be part of the future
Rather than just being driven by industries, Industry 4.0 is the transformation that consumers benefit from. It is the development of technology in manufacturing systems, increased intelligence of various components, and synchronisation of systems with rapid data transfer that defines this new era. Processes don't produce only components or products, but data too. By intelligent algorithms data is transformed into know-how and using available technology, it is used to influence and improve processes in real time.
One project initiated by Bosch, for example, a single inspection bench would check machines that carried out spark erosion of spray holes on nozzles. With the addition of intelligent sensors and RFID technology, real time analytical solutions were made available. It was now possible for the operator to closely examine the quality level of the nozzles. This real-time transparency increased efficiency and the risk of a defective part reaching the customer was reduced by predictive estimation. Industry 4.0 initiatives have not only yielded in cost saving but also quick decision support systems for people on the shop floor.
For the industry in India it is very important, that local solutions are affordable, easy to use and robust. Bosch India aims for a payback period of less than two years for such projects and is focusing on areas such as digitalisation of shopfloor management, usage of M2M connectivity, energy management, and implementation of manufacturing executing systems (MES). This will enable manufacturing to not only improve the productivity, but also create best practice solutions that can be used across diverse locations. For instance, the MES Pro Master implementation has enabled transparency among all Chassis systems plants in the international production network. At the Bosch Chakan plant this has led to an increase in OEE from 81.5 percent to 90.5 percent, thus solidifying its status as a benchmark for OEE productivity among other plants with manual lines.
(Continued on the next page)