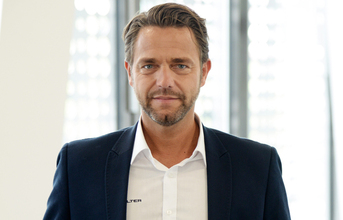
Coating determines tool life
An example of the newly developed substrate and coating technologies is the PVD-based coating (physical vapour deposition) for solid carbide tools in the Walter Prototyp Ti range. This coating substantially increases tool life in comparison with the conventional ANC coating (aluminium chromium nitride) - by up to 100 percent and more. This means that the tool life of a window frame made of 3.7164 titanium with a tensile strength of 1250 N/mm² when semi-finishing and finishing using a Prototyp HPC Ti40 has been able to be raised by 154% from 175 minutes to 444 minutes. Using a Prototyp HDC Ti38 L for finishing the outer contour has extended tool life by 116%. The speed has been increased by 25% and the machining volume by 23%.
A further innovation is CVD coating technology for the indexable insert cutting tool material WSM45X, which is used for example for the Walter BLAXX M3255 porcupine milling cutter. The coating functions as a heat protection shield, facilitating high cutting speeds of up to 65 m/min and extending tool edge life to up to 130 minutes. This makes it possible to double the tool life of titanium structural components, which are typically made using a mixture of full slotting and climb milling at a cutting speed of 45 m/min and a feed of 0.12 mm. A further option is to increase the cutting speed to 65 m/min with a constant tool life of around 60 minutes. Finish-milling can also be carried out with PCD (polycrystalline diamond) cutting edges, which are amongst the hardest materials known.
An appropriate coolant strategy must be implemented in this case, however, in order to keep the machining temperature at the cutting edge under 600 °C. In general, the cutting fluid and the concentration of the cooling medium have a significant influence, especially on tool life. It is most important to introduce the cooling medium as directly as possible into the working zone. This is facilitated by special coolant-throughs in the tools. High-pressure cooling at up to 70 bar is state of the art for new machine tools. Special tool solutions for cryogenic machining go even further, working with liquid carbon dioxide or nitrogen, which is even colder.
(Continued on the next page)