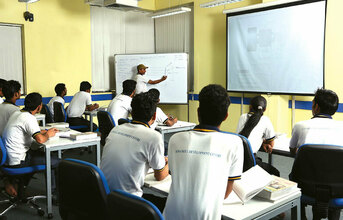
This initiative does not only emphasise on skilling but also creates opportunities. "The main goal of Skill India Program is to create opportunities, space and scope for the development of the talents of the Indian youth. No doubt Skill India program seems to be a good initiative - providing skills to people, especially because India is one of the few countries all across the world whose working age population will be very high, few years down the line, going by its ever-increasing growth of population, as per the World Bank. It Plays role of matchmaker between right talent and the manufacturing industry due salient features," points out Pravin Jadhav - Manufacturing Head, Ariston Thermo India Pvt Ltd.
In the era, where the technology is transforming with great speed, it is important for the workforce to know about the latest technology. Speaking about it, Nair adds "Technology is getting updated to provide a better quality output at a faster rate. The older systems of training have become obsolete, and with initiatives like Skill India, there is scope to add shortterm, industry-relevant skill training modules to provide exposure to the latest methods used in the industry. Not only this, technology has been adopted in training methods too - like the inclusion of simulator-based training to provide a better understanding of quality and its relation to application skills. Technology providers like Skillveri have aided industries in achieving quick ramp-up by upskilling their workforce in skills like welding and painting."
Conclusion
"Manufacturing Industry has seen tremendous transformations over past three decades. We have moved from the batch processing to continuous processing, large stocks to lean manufacturing, percent rejects to PPM to zero defect manufacturing. On every step, industry needed different skill sets. As a result, the skill gap continued to be widened. This was largely countered by big manufacturers like automotive OEM's and Tier-I companies by having their own, internal training and developdevelopment
set-ups. Going forward, manufacturing will completely change when company's embrace - what is popularly called-Industry 4.0. So, changes in how we manufacture have been happening in the past, and they will continue to take place - perhaps much bigger changes at much faster rates - in the future. To be ahead of the curve, one needs to keep pace with these changes not only through acquiring new technologies, and new manufacturing practices, but also by having a manpower which is always capable to handle the new methods," says Kapur. As a result, re-skilling becomes an essential part of training programs. "In our organisation, re-skilling is done for employees at all levels whenever a new process or product is introduced. Expert guides run them through the latest technological trends to make them suitable for the changed environment," continues Dr. Goel. Godrej also follows the similar method. "We review the skill set and identify the gap areas periodically for all the workmen in the organization. We have various training programs, conducted by internal as well as external faculty, aimed at updating the skillset of our workforce. We also give them multiple opportunities through executive courses from reputed institutes to upgrade their educational qualifications," Shariyarr concludes.
END