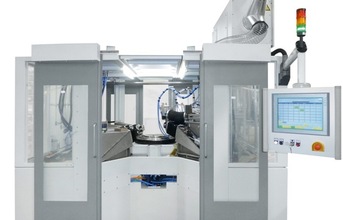
In only a few other branches of industry are development pressures as enormous as in aircraft construction. One of the reasons is the fact that legislation is getting ever stricter about the CO2emission of aircrafts at the same time as market expectations are of a rapidly accelerating growth in the sector. It is as a consequence of this development that aero engines are becoming a focal point. They need to show a reduction in fuel consumption, whilst - at the same time - having to guarantee greater propulsion values.
It is obvious that such a development has a massive effect on the components used in the engines. They are made of extreme materials that have to withstand high stresses. The question is: how can one machine these materials with speed, precision and process integrity? The Emag experts have a highly effective answer to this question: the ECM (Electro Chemical Machining) technology. Cutting processes often lose out in the decision making. The ECM machines from Emag open up new opportunities in aero engine manufacturing.
There is one important correlation to be found in the manufacture of aero engines: the higher the temperatures generated by the engine, the more efficient it is. The aircraft will consume less fuel over the same distance and increase its flying range. It is easy to imagine what this means for the materials used in the bowels of an aero engine. The higher temperatures irrevocably lead to the use of extremely hardwearing materials that perform better under stress. But that is only ‘half of the truth' as, at the same time, many components are becoming more complex and still have to be machined at the highest precision. It is the only way to achieve the targets set over a decade ago by the aero engine sector, namely a 20 percent reduction in both CO2emission and fuel consumption.