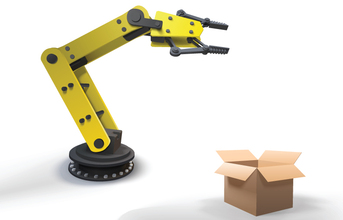
Nerurkar of TÜV SÜD says that businesses today are looking for processes and solutions which are simple to operate, reliable in terms of output, quality and flexible to change and of course, cost effectiveness. "Lean manufacturing or Just in Time (JIT) manufacturing principles are implemented to ensure that manufacturing cycle and response time to customers are as short as possible. Manufacturing processes including loading, unloading and transference to different locations are getting completely automated to ensure that operations are balanced, output is predictable and quality is measured online giving dual benefits of zero defect and lean manufacturing." Shariyarr points out that any shopfloor contains two types of flows - material flow and information flow. "Integration of these two flows encircles the complete automation, which will give real time status on product and its related data. Here automation system helps providing instant feedback for quick decision making." He explains that on the product front, the system should track the components, sub-assemblies, which move right from the suppliers to the end consumers.
"This not only builds complete traceability of the output but also helps reduce the throughput time. On the data front, it should collect all the relevant information of the process such as inventory levels, part quality, not in operation, etc. Such information will throw out wastes in the entire supply chain. This feedback/real time data shall provide the opportunities for improvement to act upon and make the processes lean."
Impact machine performance
According to Shariyarr from Godrej Appliances, machine performance is built on three major functions that are: availability rate, production rate and quality rate. Collectively defined as Overall Equipment Effectiveness (OEE). All these parameters are interconnected and industrial automation plays a major role in improving it. "Automation compiles all machine related information and converts it into fruitful real-time data. This is further analysed to respond quickly whether machine itself is going out of parameters or product quality is getting deteriorated. New machine interfaces also provide the real time wear and tear information of critical machine components, which affects productivity and quality. This can be used for taking many preventive actions well in advance to avoid a breakdown or a poor quality output. Thus automation has reached a level where man and machine can interact with each other delivering value to the organization," he explains. Varroc's Vachhani says that the manufacturing industry is always looking for ways to improve the efficiency of machines and bottlenecks in their operations. And that's where automation helps. "Industrial automation methods helps manufacturers to identify and take actions on negative factors such as unexpected downtime, equipment malfunction, production losses caused by shortage of resources and increases the overall equipment utilization rate," he says.
Bhangale from Racold Thermo underlines that automation helps to achieve single piece flow, which reduces the WIP, hence is helpful for JIT. "Consistent repeatability is achieved with automation which reduces variation in process & helps in abiding the principles of Lean Manufacturing & WCM. To optimise the result of automation it is suggested to involve lean / WCM team in designing stage, who have to work on work place origination, ergonomics, ease of Autonomous & preventive maintenance. We follow WCM in our origination, hence right from design stage of automation we activate EEM (Early Equipment Maintenance) pillar of WCM in Automation & prepare machine ledger, EVO, etc. EEM pillar also takes the inputs from WO (Work place organisation), AM, PM & logistics pillar."
(Continued on next page)