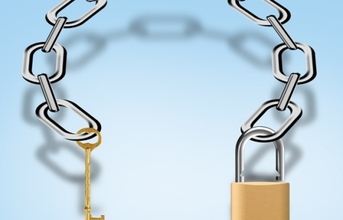
Self certified suppliers
Today, suppliers supply parts directly to the assembly points or at the point of use thus eliminating any incoming inspection or storage that minimises additional material handling and reduces the cost of quality. Regular supplier audits to ensure that processes are in control and quality systems are followed are a regular feature in many industries. Supplier's quality performance is reported at regular intervals in Parts Per Million (PPM) and sigma levels instead of percentages. Incoming quality issues are analysed to arrive at the root cause to initiate preventive actions. Original Equipment Manufacturers (OEMs) ensure and validate the effectiveness of such preventive actions through audits to ensure that similar problems do not reoccur.
Global purchasing
Companies are harvesting the benefits of volume based costing to reduce raw material costs. The movement is towards a global purchasing system that combines the requirements of all different manufacturing locations worldwide to gain volume based discounts compared to local purchasing (from different vendors) by negotiating and purchasing for each individual unit.
A leading vertical and horizontal transport manufacturing company used this approach to reduce the cost of purchase of its critical items by 15 percent to 20 percent. The travelling cable used across all its manufacturing locations was manufactured by one company. Each individual unit had initially negotiated the prices for their volume requirements. The company paid different prices in different parts of the world for the same product. Negotiating with the travelling cable supplier for a global purchase order, the company lowered the ‘travelling cable' cost by 15 percent to 20 percent.
Logistics optimisation
Organisations are relooking at logistics to reduce both the cost and lead time and in the process reduce environmental impacts. Logistics routes are being reviewed and optimised. The concept of milk run is used effectively by companies to get materials in kits at regular intervals, directly to the assembly lines. This saves time by consolidating materials in the plant by the operators.