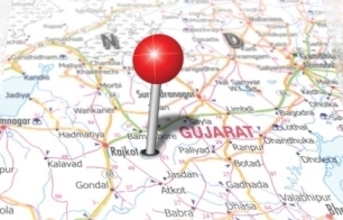
Industrial estates
Gujarat Industrial Development Corporation (GIDC) was in 1962 to accelerate industrialisation in the state. It began by identifying locations for industrial development and creating necessary infrastructure in these areas. This led to the formation of industrial estates. The intention was to provide facilities such as roads, drainage, electricity, water supply, factory sheds, and other infrastructural amenities etc in a way that manufacturers can straightaway focus on their work at hand. "The first industrial estate in India, Umakant Pandit Undyog Nagar, came up in Rajkot, in September 1955," says Tejura, and it became a huge success.
Industrial estates played a particularly positive role in developing the industrial activity and prosperity in the country per se. Yet, for Rajkot, government supported industrial estates haven't been such a nice experience. "Government initiatives, be it in providing land for manufacturing, water for industrial purposes, or supportive policies for the manufacturers, have been dismal.
Industrial estates are a failure when it comes to the government owned ones. The privately managed ones gets things done but suffer due to lack of infrastructure - roads, drinking water, etc. The villages in which some of the largest estates are located don't have Nagar Pallikas but Gram Panchayats, reducing their budget allocation for development. There is absolute lack of political will and the bureaucracy makes it worse, when it comes to infrastructure in Rajkot," says Patel.
Anilbhai P. Bhoraniya, Vice President, Shapar Veraval Industrial Association, one of the largest in the region, explains that Shapar and Veraval came together and combined their resources to jointly develop the area for the manufacturing industry. It hosts some important large scale and medium scale manufacturing units including that of Mahindra & Mahindra and employs about 2-2.5 lakh wage earners.
"We recently got permission and financial support for constructing an over bridge across the highway dividing Shapar and Veraval. This is estimated to cost around Rs 40 crore and was long due to remove the bottleneck created by traffic issues and lack of proper roads. We are now working to solve drinking water issues, to install our own fire brigade station, and a government supported pharmacy for the people employed in the estate," informs Bhoraniya.
Mohit Dobaria of Accurate Technocast Pvt Ltd, which is a medium scale auto component manufacturing unit in the Shapar Veraval Industrial Estate considers himself fortunate to have his unit here. "Drinking water is a major problem in these areas but we get a lot of support from the association in solving imminent problems that creep up during the daily running of business. We don't have to worry about power and electricity, skilled workers are easily available, and there's camaraderie among the same industry manufacturers that helps us tackle any short term problem. It is so convenient to have your unit located in one of these estates, why would anyone want to have it outside, and be all on your own," he opines.
Industrial estates were conceived to promote small-scale industries by providing infrastructure and other amenities, by improving operational efficiency through common facilities and knowledge accumulation, and through collective interest of entrepreneurs on the same interest area. In Rajkot, all these and more have been provided by private industrial players, rather than by government initiatives.
Availability of workers and skilled labourers
It is the inherent nature of the Rangila Rajkotians to take the plunge into entrepreneurship and commerce. "Working for others is not in our blood," says Kakadiya. "This makes it difficult to find daily wagers from around the place, although the rural neighbourhood does supply some".
The workforce for these industrial cores actually comes from UP and Bihar, people who migrate for work, he explains. "When the government started the 90-day employment for all policy, it made life a little easier for us to get ready labour, but the issue remained that by the time they got trained, they were ready to leave. After the 90 days engagement, they'll prefer to go back to their villages to take care of their crops and household. For us, the demand and supply of labour becomes hard to match," says Kakadiya.
Over the last few years, manufacturers have moved to advanced machineries that are less labour intensive. The CNC machines need one operator while the lathe machines needed four. Although the CNC machine operator demands four times the salary of the lathe machine operators, they are also willing to work the extra hours during times of high demand, enabling an amiable solution to sickening labour unavailability.
More than numbers, the leaders of the industrial associations are worried about the potential of the workers. "There is an acute need of training and education among the people here. There are over a 1000 units manufacturing auto components here in Rajkot and they export their products to big companies but our colleges do not have a single curriculum running on automobile engineering. The same goes for ceramic engineering, leather and textile industry faced courses, and so on." It is imperative that the educational institutions in Rajkot are motivated to start industry facing courses to educate and train the young force looking forward to join the family business.
The People - Rajkot's greatest resource
Despite all the infrastructural problems around the town, and more than any other resource possessed by the region, it's the human resources of Rajkot that yields gold. The people of Saurashtra and Rajkot region are known for their hard work, honesty, and talent in workmanship. According to the 2011 census, the urban area of Rajkot has a total population of 1,286,678 and the average literacy rate is 87.80 %, which is higher than the national average (82.20%).
Patel exclaims that Rajkot is like mini-China; every single item that any industry needs is manufactured here. People in this region are extremely hardworking and have a knack towards craftsmanship. Although the general education among the people here is only till the 11 or 12th grade, innovation is more rampant in this part of the country, and even goes unnoticed.
Tejura echoes the mood. "Show us any new piece of engineering, and we will make it in less than 10 days," he says exuberantly. Yet these small and middle class manufacturers do not get the reward they deserve for their talents because of their lack of education, awareness, and government support. To show an example, Tejura speaks of the three wheeled tractor innovated by a small time agricultural equipment manufacturer, which is being used in the farms in the state for the last ten years with great success. "While normal tractors would cost you anything above Rs 5 lakhs, this three wheeled tractors cost less than Rs one lakh; yet the government is not awarding it the due registration as a tractor because traditionally tractors have four wheels. Hence, this product is still not in the market and the innovator cannot have any kind of recognition. Instead of coming forward and promoting this kind of technology and innovation and help develop the core sectors in the country, the government is sitting on the files and the paper works for the last ten years", he adds.
Speaking to several proprietors of the small and medium sized manufacturing units in the region makes one thing clear - they are concerned about the work - the quality and the quantity of it, the orders they receive, the process of production and delivery. The fringe aspects of marketing, or promoting their products, advertising and creating brand values, streamlining processes of production and management, and even for that matter, crafting wise pricing policies are often neglected.
"The people here are too honest. They live by their words and the quality of their works. This is one reason we are trusted all over the world", claims Patel. Look at this from a different angle, and you will see how the same manufacturers get exploited, says Tejura.
He cites an example when he asked one of the traditional jewellery manufacturers cite double the price to a foreign client, who felt the deal was still so very cheap. "This is true of all the industries in Rajkot. Smarter process management can further reduce the manufacturing cost and there is so much scope to export and cater to a wider market, to earn a better price for the products," he says.
(Continued on the next page)