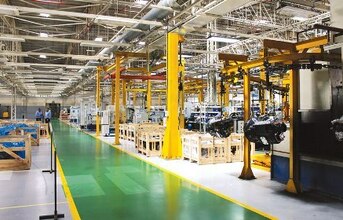
The strategy
Managing cost at the shopfloor level has been one of the key reasons for the Group's growth in a very competitive market. "Besides growing capacity ahead of the market, we have also focussed on localisation. This has helped us keep the manufacturing cost low.
"Secondly, I am able to leverage this low cost at the global level. For example, if a product is getting manufactured at 30x cost in another Eaton plant and the Ranjangaon plant is manufacturing the same product at 25x cost then it puts us in an advantageous situation. And we have been able to achieve this cost competitiveness in a consistent manner."
KK shares that from a shopfloor level point of view, the Ranjangaon plant has been able to achieve high levels of operational efficiencies by doing what he describes as a ‘lot of classical activities'. These ‘classical activities' activities involve the global manufacturing best practices like lean, kaizen, Gemba walks and so on implemented by the Ranjangaon plant while taking into consideration its specific requirements.
For example, the Plant ensures that it captures all product requirements in VSM (Value Stream Mapping). "It starts with the analysis of the requirement and the given scenario. Then, we plan and work out the next in line series of events in such way that there is optimisation of the resources without compromising on our fundamental values like quality, safety and productivity," KK says. He adds that the whole process is driven by three aspects: self sufficiency & sustainability, localisation and making at the right cost.
According to KK, the Ranjangaon plant - like any other Group plant - also encourages employees to be part of the continuous improvement process. "For example, we have something called as the Rapid improvement events (RIE) wherein the involved team is empowered to implement quick ideas to improve the current levels of output (in terms of productivity and quality). In fact, the decisions are made at the shopfloor level then and there. At the next level, we have cross functional teams that identify improvement areas and work accordingly. Big investment related decisions are obviously at the higher levels but the management is extremely open and cooperative to any idea that will lead to improvements," he explains.
These initiatives are certainly working since the plant has seen dramatic improvements across many areas. KK shares the example of a six speed assembly line. "Earlier, we were producing about 25 transmissions on one of these six speed assembly lines. With improvements, we are now producing 70 transmissions on the same line. And this has been achieved in the same space and the same equipment with lower manpower. Like that we have multiple lines where we have brought huge improvements," he shares.
(Continued on the next page)