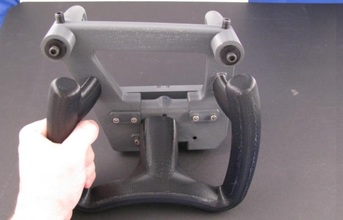
Another advantage of direct digital manufacturing is improved functionality. Since the additive process can easily produce organic shapes that sweep and flow, the tool designers can maximize performance while improving handling characteristics.
"The layered FDM manufacturing process is well suited for the production of complex bodies that, when using conventional metal-cutting processes, would be very difficult and costly to produce," says Eidenschink. An example is a tool created for attaching bumper supports, which features a convoluted tube that bends around obstructions and places fixturing magnets exactly where needed.
The jigs and fixtures department has developed a simple flow chart to determine when FDM is a fitting option. The criteria are temperature, chemical exposure, precision, and echanical load. With Stratasys ABS material, which the engineers find comparable to polyamide (PA 6), many tools for vehicle assembly satisfy the criteria.
For those that do, designers can create devices that Capitalise on all the advantages of the additive process. Both Schmid and Eidenschink believe that no enterprise can afford to do without rapid prototyping for product development. Yet, they see so much more possibility. "FDM is taking on increasing importance as an alternative manufacturing method for components made in small numbers," says Schmid.
Source: Stratasys
END