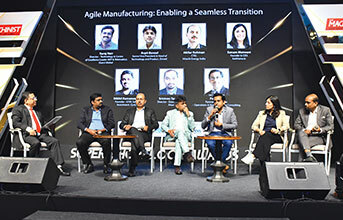
Moderated by Pallab De, Partner and Leader – Operations & Manufacturing Consulting, A&D PwC, the panel comprising Akilur Rahman, CTO, Hitachi Energy India; Arpit Bansal, Senior Vice President & Head of Technology and Product, DriveX; Nikhil Ramaswamy, Founder - GTM, Sales, Investment, CynLr; Sonam Motwani, Founder & CEO, karkhana.io; Srinivas Tangudu, Director - Data Analytics, Altair; Suraj Nair, Director – Technology & Centre of Excellence Leader (IOT & Telematics), Quest Global discussed how digital transformation fosters flexible production, rapid customisation, swift market adaptation, and efficient resource use, creating a responsive and dynamic manufacturing landscape.
Pallab De kickstarted the discussion by posing a question to Suraj Nair about specific examples of how IoT has significantly improved manufacturing efficiency, flexibility, and agility. In response, Suraj Nair cited a recent example involving a food and beverage manufacturer seeking to digitally transform its production facilities. "This manufacturer faced common issues related to the segregation of OT (Operational Technology) and IT (Information Technology) and sought ways to enhance operational efficiency through digital transformation, where IoT played a crucial role," he added.
Nair explained that IoT could be viewed from two perspectives: the non-human and the human aspects. "From the non-human perspective, IoT involves communicating with equipment and systems to extract data, which can then be stored and used for future engineering and analytics to better understand the production facility's state. The human aspect focuses on how this data helps reduce the cognitive load for workers on the shop floor."
Further he emphasised that IoT bridges the gap between OT and IT by extracting data from various equipment, which often differ even within the same manufacturing company. This data extraction involves integrating with proprietary protocols, converting the data into a usable format for the IT network, and sometimes retrofitting sensors to legacy equipment to gather sufficient information. Nair also acknowledged that this process might face resistance from OT professionals but is necessary for obtaining actionable insights.
He highlighted the role of real-time data in making the shop floor more comfortable for workers by providing timely information through devices like smart glasses or mobile handsets with AI integration. Additionally, IoT also enhances safety by monitoring workers' proximity to hazards and analysing air quality using computer vision.
Later Nair elaborated about the challenges of implementing IoT technology and how they are addressed. He identified the diversity of equipment and the resistance to change as significant challenges. "Different locations often use different types of equipment, requiring new integration methods. Additionally, long-time shop floor workers might resist transitioning from manual data entry to using digital devices and dashboards. Overcoming these challenges involves training and demonstrating the benefits of the new systems to improve productivity and ease of work."
The discussion moved to Srinivas Tangudu, who was asked about the utilisation of digital twins in process optimisation and predictive maintenance in agile manufacturing. Tangudu explained that a digital twin is a digital replica of a physical counterpart, such as an asset, plant, machinery, system, or process. It allows real-time performance simulation and decision-making to optimise and enhance the quality of manufacturing output.
He shared use cases such as real-time asset monitoring during the COVID-19 pandemic and predictive maintenance, which replaces the traditional scheduled or reactive maintenance approaches. Tangudu highlighted that digital twins are crucial for agile manufacturing, helping companies meet sustainability goals and optimise processes. By real[1]time monitoring and simulation, companies can ensure efficient energy use and compliance with environmental standards.
Pallab De then asked Akilur Rahman about how agile manufacturing practices contribute to the faster development and deployment of green technologies or new products. Rahman emphasised the importance of a vision, citing the net-zero or carbon-neutral targets set by countries and corporates. He mentioned India's goal to achieve 500 gigawatts of renewable energy by 2030 and the backcasting required to meet this target, involving significant manufacturing and supply chain efforts.
Rahman explained that long lead items like transformers require extensive time for manufacturing and assembly, highlighting the importance of integrating digital twins and simulation in the design, planning, manufacturing, and operation phases. Digital twins enable companies to predict and address issues promptly, ensuring reliability and performance. He noted that industry 4.0 and the energy transition demand more agility in manufacturing processes, combining process analytics and data analytics to enhance agility.
Lastly, Pallab De directed a question to Arpit Bansal about how agile manufacturing supports circular economy practices and the remanufacturing of pre-owned two-wheelers. Bansal defined agility as flexibility in delivery, focusing on affordability for customers. He explained that their goal is to refurbish the two-wheelers cost-effectively, catering to customers who otherwise couldn't afford them.
Bansal emphasised the importance of digital systems that provide real-time feedback from customers to the manufacturing plant, enabling quick and cost-effective refurbishments. He stressed that agility involves fixing only what the customer demands, ensuring affordability and meeting specific requirements. For instance, customers looking for stability and mileage in a reused vehicle have different needs compared to those seeking a high-performance riding experience.
Finally, Sonam Motwani discussed the trends and challenges in agile manufacturing, particularly for MSMEs. She emphasised the need for tools and technologies that can be easily adopted by smaller manufacturers to enhance capacity and capability. Motwani provided an example of how her company, Karkhana, leverages data and machine learning to expedite the quotation process for design changes, thereby improving supply chain efficiency and responsiveness.
In conclusion, the panelists highlighted various aspects of agility in manufacturing, emphasising the role of IoT, digital twins, and real-time data in enhancing efficiency, flexibility, and sustainability. They also discussed the challenges of implementing these technologies and the strategies to overcome them, underscoring the importance of training, digital integration, and customer-centric approaches in achieving agile manufacturing.