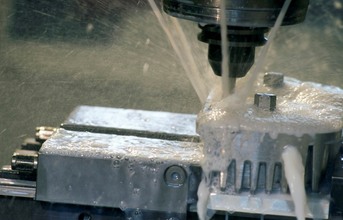
Peter is also a keen mountain biker, so in the early day of having the new Haas mill he kept it busy and practiced his design skills by creating a range extender to fit Shimano 11-speed cassettes. As with the VW tuning parts the Shimano ring is cut from solid billet, after which it's anodized black. It may not be the company's core business, but it's an example of how creative minds will always find work for their tools.
"The machinist we hired originally specified the Haas VF-3," says Peter. "It's a very useful machine but after he left we quickly discovered we needed the VF-2SS with its higher spindle speeds. We take advantage of the long table on the VF-3 and load it up with as many parts as possible. However, our eventual aim is to upgrade it to another VF-2SS."
In the meantime, both Haas machines have also enabled the company to make better prototypes of new products. "We kind of use the Haas machines as 3D printers," says Peter. "For example, we rough cut new brake calipers which we then use for fitment tests. Although the final product is cast, machining the first versions in aluminium is so much quicker and easier."
The finished parts themselves may not be authentic, but CSP tries to maintain an authentic final look wherever possible. For example, one of the company's brake brackets allows a customer to dispose of original drum brakes and mount much more powerful disc brakes, whilst still keeping the traditional, five-bolt wheel pattern typical of 60's VWs.
Valve covers are another mainstay CSP product. The originals are tin fabrications. The CSP valve cover is machined from solid and is available anodised in a variety of different colours. The improved product prevents leaks, improves cooling and dampens noise. Of course, it looks great, too! Previously, the throttle linkages were made by the subcontractor and cost CSP €9 each. Now, they're made in-house and cost €5!
"We make around 500 off, which is unusually high for us. Typically, we make around 10-100 of a part, for stock. So many of our parts were once welded steel fabrications and now they are machined from solid. We also like to scan parts and re-engineer them from the models. It's a very fast and effective way to get something new into production. We may invest eventually in a 5-axis Haas, so we can port cylinder heads. That's the direction we're headed: more complex parts."
Adjacent to the Haas CNC machines on what appears to be an enormous flat, steel machine table sits Peter's latest obsession: a split-screen VW Transporter, which CSP is rebuilding. As yet unpainted, the 1960s vintage ‘Bus' will eventually sport the same colours as the dragster and will be used as the team support vehicle, as well as serving as an additional test bed for new and prototype parts. Also like the dragster, it will be built to fly.
As we stand and admire this latest project Peter hands me a brake bracket: "One more, simple thing we now do that we didn't do before," he says. "We engrave part numbers on our products. It doesn't sound much, but engraving, rather than stamping numbers manually, is far quicker and the end result looks so much more professional.
He smiles: "That just about sums it up, really. The Haas machines have helped us to make all of our products better, find new parts to make and generally improve everything we do."
The author works for Haas Automation Inc.
END