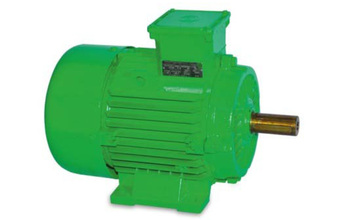
Bharat Bijlee's SynchroVERT motor
Electric motors are estimated to consume about 65% of the electrical energy consumed by industry. Energy costs over the typical life cycle of a motor can be as high as twenty times the original capital cost of the motor. Energy efficient motors thus offer an opportunity to significantly reduce energy costs and their collateral environmental effects.
Increasingly, there is a strong economic - and environmental - case for choosing high efficiency motors over conventional ones. Instead of repairing or rewinding a failed motor, organizations may profitably consider replacing them with energy efficient motors or motor driven systems; this can bring about significant reduction in energy consumption.
In the last two decades motor efficiency measurement standards have undergone extensive changes. At the same time, technological advances and greater end-user awareness have resulted in higher availability and application of energy efficient motors, particularly IE2, IE3 and now even IE4.
However in most continuous running plants, the installed base of motors is already over 10 years old, inefficient, oversized and operating on fluctuating load between 40%-80% without a Variable Frequency Drive. Rewound motors also cause a 10 to 15% loss of power.
Motors in the Plastics Industry
The plastics industry uses a large number of electric motors. Since energy costs form a significant component of the production costs in a plastic plant, plant managers and machine designers are constantly looking for energy savings solutions.
Some of the manufacturing machines where smaller rating motors are used in the plastic plants are:
- Haul off application in pipe extrusion machines
- Various blowers and pumps in extrusion machines
- Main extruder in plastic blow moulding machines
- Winder/un-winder application in plastic blown film and plastic tape winding machines
- VDP pump application in plastic injection moulding machines
- Piston pump application in blow moulding machines
- Mould/oil chillers used in plastic machines
- Cutters used in plastic pipe and film extrusion machines
- Main motor in circular plastic tape winding machines
- Plastic auxiliaries/ancillaries like feeders, driers, conveyors etc.
- Compressors used in plastic plant
(Continued on next page)