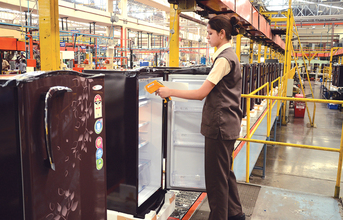
Structured approach
A next step to this is an organised approach which is driven by a structured, tailor-made roadmap, a methodology for implementation and a comprehensive review mechanism. Key inputs, training, and guidance are provided by a mentor, supported by counsellors.
Participating companies are required to form a cluster organisation with clearly defined roles and responsibilities. The organisation should ensure the involvement of people at all levels. There must be designated authorities like cluster CEO, coordinator, deputy coordinator and cluster officers, to take decisions and implement those decisions quickly. The cluster CEO is generally empowered to implement the outcomes. It would be in the interest of an organisation if the CEO is a role model who can inspire the team to work towards a common goal. The cluster roadmap is not predefined and it cannot be applied randomly. It is created by the mentor in consultation with the Cluster CEOs, after assessing each company in its
current state. While the roadmap is common to all companies participating in a particular cluster, care is taken to ensure that each of them benefits to the maximum. The cluster roadmap is valid for a specific period of time, usually two years. However, the duration can depend on the number of modules in a
particular cluster.
Objectives of a Cluster
The underlying philosophy of a cluster is ‘Getting together, learning together, achieving together'. With this philosophy as a foundation, a cluster program aims to achieve the following:
- Make factories visual and safe
- Bring total employee involvement
- Bring quality focus
- Install material flow and reduce inventory
- Greening the supply chain - zero waste, reduce carbon footprint
- Profit improvement
- Building capabilities within employees
- Building a culture of continuous improvement, continuous learning and sustaining all improvements
Case study : Godrej Cluster Journey
Godrej Appliances was among the first few companies in India to join the hybrid cluster formed by CII in May 2010, where for the first time OEMs from different industries participated. A hybrid cluster has the potential for breakthroughs in the operation, production and distribution cycle. For example, the company benchmarks processes of companies from different industries, both manufacturing and non-manufacturing. In cross-industry benchmarking, a company engaged in, say, white goods, can adopt processes from a company dealing in heavy equipment and thrive in a new business environment.
(Continued on next page)