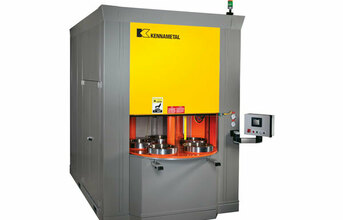
Manufacturers and quality professionals in such industries as automotive, aerospace, energy, medical, and others requiring high-precision components know that removing particle left at intersected holes and ensuring no micro contamination is a quality challenge that cannot be overlooked. Customised complex valves, gears, pinions, and thousands of components can be machined in seconds but can take minutes to get finish completely. Production bottlenecks, increased costs, and longer time to market are among the results.
Kennametal Extrude Hone is dedicated to providing Precision Surface Solutions for component of uncompromising quality. Proprietary technologies such as TEM (thermal energy machining) are solving increasingly complex finishing challenges faced by manufacturers around the world.
Delphi-TVS is a joint venture between Delphi Corp. (Troy, Michigan USA) and TV Sundaram Iyengar & Sons (Kancheepuram, India). Delphi is the largest automotive supplier in the world and Delphi-TVS is the largest automotive systems manufacturer in India.
"Being a global company, we have a great responsibility to maintain world-class quality standards in our products," says TN Umasankar, head of the Delphi-TVS manufacturing engineering department. "We manufacture diesel fuel injection parts - high-volume components. The main issue is burr removal on cross-sectional holes from previous machining operations."
Delphi-TVS faced many issues: High component volumes approaching a million a year made hand-deburring unaffordable and the high-precision nature of diesel fuel injectors made TEM solution a necessity.
After much investigation, the company chose Kennametal Extrude Hone's TEM (thermal energy method) solution. A pressurised mixture of a combustible gas and oxygen is injected at 5 to 10 atmospheres of pressure into a containment chamber sized both by the amount of material to be removed and the volume of parts in the chamber. An ignition system ignites the gas mixture, releasing heat energy from the oxidation of fuel in a 20-millisecond, high-speed energy wave. With their raised surface areas and thin cross-section features, even internal burrs and flashings burn away instantly. Because the gas mixture engulfs the entire workpiece, all internal and external surfaces are exposed to the rapid oxidation. Internal cross-drilled holes and intersecting edges that are difficult or impossible to reach are instantly processed.